实验一 典型零件的热模锻分析
一、实验目的
培养学生综合利用DEFORM有限元软件进行金属塑性成形加工手段的模拟能力。
二、实验任务
(1) 熟悉DEFORM有限元软件的操作命令。
(2) 通过热模锻有限元模拟成形过程,了解热模锻的工艺特性,熟悉热模锻模拟前处理、求解和后处理等操作过程。
(3) 通过热模锻有限元模拟成形过程,了解工件在成形过程中的应力变化情况,工件几何尺寸的变化情况等。
三、实验要求
(1)实验报告需写上初始设置参数,如总模拟步数、模拟计算步长、对象网格数、对象材料、运动速度、摩擦系数等相关资料。
(2)实验报告上配有相应的分析结果模拟图及数据。
四、实验步骤
4.1 问题描述与分析
以DEFORM软件提供的几何体作为工件和模具,构成热模锻的分析对象,其中模具材料为热作模具钢,工件从加热炉中取出的初始温度为1000~2000F。(具体温度值由个人自己确定)
非等温热模锻仿真过程不仅要模拟模锻过程,还要模拟热传导过程。因此,整个仿真模拟过程分为以下三个阶段进行:
(1)第一个模拟阶段——热传导过程:工件加热后移动到模具的过程中,在空气中的移动时间为5~30秒(具体数值由个人自己确定),该阶段工件与外界环境发生热传导。
(2)第二个模拟阶段——热传导过程:工件移至到下模上后,在进行锻造之前,停留在下模具上的时间为2~10秒(具体数值由个人自己确定),该阶段工件与下模发生热传导。
(3)第三个模拟阶段——模锻过程:工件在上、下模作用下被锻压变形。
在分析过程中根据轴对称性,选择工件和模具的1/4对称面来进行分析,以此减小模拟时间。
4.2 第一个模拟阶段——工件与外界环境热传导模拟
1.创建新项目
打开DEFORM软件,进入DEFORM前处理界面。
2.设置模拟控制初始条件
注意:设置模拟计算步长:在“Solution Step Definition”栏中选中“With Time Increment”,下拉菜单中选择“Constant”,其输入栏中输入相应值,该值=
。
3.输入对象模型
4.划分网格
注意:第一模拟阶段中,仅有工件与外界环境发生热传导,因此只对工件进行网格划分。
5.定义材料
6.设置热传导边界条件
第一模拟阶段中,仅有工件与外界环境发生热传导,因此只需对工件设置热传导边界条件,即进行工件的上表面、下表面、圆柱面的热传导边界条件设置。
7.生成数据库文件及分析求解
8.后处理
4.3 第二个模拟阶段——工件与下模热传导模拟
1.加载数据库
进入前处理界面,弹出的对话框,询问要打开数据库中的第几个模拟步,此处选择最后一步。
激活对象树中的工件,使其高亮显示,打开
对话框,在“Temperature”栏显示目前系统默认的温度值不再是设置的初始温度。
2.设置模拟控制初始条件
注意:设置模拟计算步长:在“Solution Step Definition”栏中选中“With Time Increment”,下拉菜单中选择“Constant”,其输入栏中输入相应值,该值=
。单击
按钮,退出模拟控制菜单。
3.对象间定位
该模拟阶段中,工件位于下模上,即需要将工件移动到了下模的上表面。
4.设置模具属性
该模拟过程中,工件与下模发生热传导,因此需要设定模具的温度。
5.模具网格划分
6.定义模具材料
7.设置热传导边界条件
进行上模的上表面、内表面、圆柱面,即除了上模两个对称面以外的所有表面的热传导边界条件设置
进行下模的上表面、下表面、圆柱面这三个表面的热传导边界条件的设置。
8.设置对象间关系
该模拟阶段只分析工件与下模之间的热传导过程,因此仅涉及传热问题,而不存在摩擦问题。
9.生成数据库文件及分析求解
10.后处理
4.4 第三个模拟阶段——模锻过程
1.加载数据库
进入前处理界面,弹出数据库中模拟步选择对话框,询问要打开数据库中的第和个模拟步,此处选择最后一步。
2.设置模拟控制初始条件
注意:设置模拟计算步长:在“Solution Step Definition”栏中选中“With Die Displacement”,下拉菜单中选择“Constant”,其输入栏中输入模拟计算步长,该值为工件最小单元边长的1/3。
3.对象间定位
该模拟阶段中,上模向下移动到工件上表面,即工件与上模存在接触关系。
4.设置变形边界条件
前两个阶段设置了热传导边界条件,该模拟阶段涉及工件的变形,因此需要设置变形边界条件。
(1)选择工件的两个对称面完成变形边界条件设置
(2)设置模具的变形边界条件
1)选中上模的两个对称面完成上模的边界条件设置。
2)选中下模的两个对称面完成上模的边界条件设置。
5.设置驱动条件
设置上模的位移驱动。
6.设置对象间关系
同时设置摩擦和热传导关系。
7.生成数据库文件及分析求解
8.后处理
五、思考题
1、网格划分大小对仿真过程的影响?
2、步长设置对仿真分析过程的影响?
实验二 挤压过程模拟分析
一、实验目的
培养学生综合利用DEFORM有限元软件进行金属塑性成形加工手段的模拟能力。
二、实验任务
(1) 熟悉DEFORM有限元软件的操作命令。
(2) 通过有限元模拟成形过程,了解工件在成形过程中的应力变化情况,工件几何尺寸的变化情况等。
三、实验要求
(1)实验报告需写上初始设置参数,如总模拟步数、模拟计算步长、对象网格数、对象材料、运动速度、摩擦系数等相关资料。
(2)实验报告上配有相应的分析结果模拟图及数据。
四、实验内容
对挤压过程仿真过程 进行以下分析:
(1)进行变形分析;或变形+热分析。
(2)调用DEFORM软件安装目录下的C:\DEFORM3D\V6_1\LABS中的几何体,DEFORM软件提供以下5组几何体:
1)工件——nut-cutoff;模具——nut-die1;nut-punch1,如图1所示。
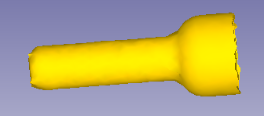
(a)组合模型 (b)分析结果
图1 工件与模具几何体1
2)工件——nut-cutoff;模具——nut-die2;nut-punch2,如图2所示。
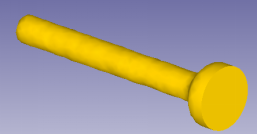
(a)组合模型 (b)分析结果
图2 工件与模具几何体2
3)工件——nut-cutoff;模具——nut-die3;nut-punch3,如图3所示。
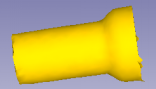
(a)组合模型 (b)分析结果
图3工件与模具几何体3
4)工件——nut-cutoff;模具——nut-die4; nut-punch4,如图4所示。
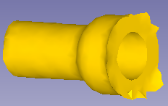
(a)组合模型 (b)分析结果
图4 工件与模具几何体4
5)工件——nut-cutoff;模具——nut-die5;nut-punch5,如图5所示。
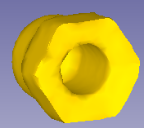
(a)组合模型 (b)分析结果
图5 工件与模具几何体5
(3)设置各相关数据。
(4)提取分析结果的变形图及数据图。
五、思考题
1、相对网格划分、绝对网格划分、局部细划的区别?
2、在设置驱动条件时,驱动类型、运动方向和运动速度的设置对仿真过程的影响?