基 础 篇
第1章 常用数控机床简介
数控机床的研制最早始于美国。1948年,美国帕森斯公司(Parsons Co.)在完成研制加工直升机浆叶轮廓用检查样板的加工机床任务时,提出了研制数控机床的初步设想。1949年,在美国空军后勤部的支持下,帕森斯公司正式接受委托,与麻省理工学院伺服机构实验室(Servo Mechanism Laboratory of the Massachusetts Institute of Technology)合作,开始数控机床的研制工作。经过三年的研究,世界上第一台数控机床试验样机于1952年试制成功。这是一台采用脉冲乘法器原理的直线插补三坐标连续控制系统铣床,其数控系统全部采用电子管元件,其数控装置体积比机床本体还要大。后来经过三年的改进和自动编程研究,该机床于1955年进入试用阶段。此后,其他一些国家(如德国、英国、日本、前苏联和瑞典等)也相继开展数控机床的研发和生产。1959年,美国克耐·杜列克公司(Keaney & Trecker)首次成功开发了加工中心(Machining Center),这是一种有自动换刀装置和回转工作台的数控机床,可以在一次装夹中对工件的多个平面进行多工序的加工。但是,由于价格和其他因素的影响,直到20世纪50年代末,数控机床仅限于航空、军事工业应用,品种也多为连续控制系统。到20世纪60年代,由于晶体管的应用,数控系统进一步提高了可靠性,且价格下降,一些民用工业开始发展数控机床,起初多数为钻床、冲床等点定位控制的机床,后来逐渐扩展到数控车床、数控铣床,以及加工中心等高性能的数控机床。
数控机床的种类非常多,常用的主要有数控车床、数控铣床、加工中心,以及电火花线加工机床等。
1.1 数控车床
数控车床是应用最广泛的数控机床之一。主要由床身、主轴箱、刀架、进给系统、冷却和润滑系统等部分组成。通常用于加工轴类、盘类等回转体零件,可实现端面、内外圆柱面、圆锥面、成形表面、螺纹类、槽类,以及孔类等工序的切削加工。常用的数控车床主要有卧式数控车床和立式数控车床。
立式数控车床,如图0-1所示,主轴垂直于水平面。该机床主要用于加工径向尺寸相对较大,轴向尺寸相对较小的大型复杂零件。立式车床分为单柱式和双柱式两种。
(a)双柱式 (b)单柱式
图0-1 立式数控车床
卧式数控车床,主轴平行于水平面,可分为平床身数控车床和斜床身数控车床两类。平床身数控车床,又称为经济型数控车床,如图0-2所示,床身导轨与水平面平行。斜床身数控车床,如图0-3所示,床身导轨与水平面之间倾斜一定角度,通常倾角为45度,在机床布局、刚性、精度,以及排屑能力方面,都优于平床身数控车床。卧式车床应用非常普遍,工艺范围也非常广泛,能进行多种表面的加工,还可以进行钻孔、扩孔、铰孔、攻丝等。
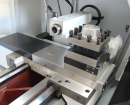
(a)外观 (b)床身导轨平行于水平面
图0-2 平床身数控车床
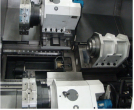
(a)外观 (b)床身导轨与水平面之间倾斜45度
图0-3 斜床身数控车床
1.2 数控铣床
数控铣床应用非常广泛,主要由床身、主轴箱、工作台、进给系统、冷却和润滑系统等部分组成。通常用于加工平面类、变斜角类,以及曲面类零件,可实现铣削、镗削、钻削,以及攻螺纹等工序的切削加工。常用的数控铣床主要有立式数控铣床、卧式数控铣床和立卧两用式数控铣床。
立式数控铣床,如图0-4所示,主轴垂直于水平面,是数控铣床中常见的一种布局形式,应用范围广泛。该机床主要采用铣削方式加工工件,能够进行外形轮廓铣削、平面或曲面铣削及三维复杂型面的铣削,在数控加工中占据了重要地位。立式数控铣床按坐标控制方式可分为:
(1)工作台纵、横向移动并升降,主轴不动方式;
(2)工作台纵、横向移动,主轴升降方式;
(3)龙门架移动式,即主轴可在龙门架的横向与垂直导轨上移动,而龙门架则沿床身做纵向移动,如图0-5所示。
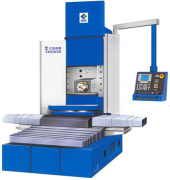
图0-4 立式数控铣床 图0-5 龙门式数控铣床 图0-6 卧式数控铣床
卧式数控铣床,如图0-6所示,主轴轴线平行于水平面,主要用来加工箱体类零件。为了扩充功能和扩大加工范围,通常采用增加数控转盘或万能数控转盘来实现4轴或5轴加工。这样,可以加工出来工件侧面的连续回转轮廓,而且,工件在一次装夹中,可以通过转盘改变工位,进行四面加工。
立卧两用式数控铣床,如图0-7所示,主轴轴线方向可以变换,即可进行立式加工,又可进行卧式加工。即一台铣床同时具备立式数控铣床和卧式数控铣床的功能。这类铣床适应性强,适用范围广,生产成本低。立卧两用式数控铣床靠手动和自动两种方式更换主轴方向。有些立卧两用式数控铣床采用主轴头可以任意方向转换的万能数控主轴头,使其可以加工出与水平面成不同角度的工件表面。还可以在这类铣床的工作台上增设数控转盘,以实现对零件的“五面加工”。
图0-7 立卧两用式数控铣床
1.3 加工中心
加工中心是在数控铣床的基础上发展起来的,适用于加工复杂零件的高效率数控机床,是目前世界上产量最高、应用最广泛的数控机床之一。加工中心一般具有刀库和自动换刀装置,刀库中存放着不同数量的各种刀具或检具,在加工过程中由程序自动选用和更换,可在一次装夹中通过自动换刀装置改变主轴上的加工刀具,从而实现铣削、镗削、钻削、攻螺纹和切削螺纹等多种加工功能。工件一次装夹后能完成较多的加工内容,加工精度较高,能完成许多普通设备不能完成的加工,非常适用于形状较复杂,精度要求高的单件加工或中小批量多品种生产。为新产品的研制和改型换代节省大量的时间和费用,从而能显著提高企业的竞争能力。
根据主轴在空间的状态,加工中心可分为的立式加工中心(主轴在空间处于垂直状态)、卧式加工中心(主轴在空间处于水平状态),和复合加工中心(主轴可作垂直和水平转换,又称为立卧式加工中心)。
立式加工中心,如图0-8所示,适合于加工有端面结构或周边轮廓加工任务的零件,如盘盖、板类零件。零件或安装在工作台夹具上,或夹持在虎钳或卡盘或分度头上。卧式加工中心,如图0-9所示,适合于对在一次安装中,有多个加工面加工任务的零件,工件往往安装在回转工作台上,如对安装在回转工作台上的箱体类零件的多个加工面的加工。复合加工中心可以在一台设备上可以完成车削、铣削、镗削和钻削等多种工序加工,可代替多台机床实现多工序的加工。
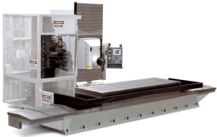
图0-8 立式加工中心 图0-9 卧式加工中心
1.4电火花加工机床
电火花加工是利用浸在工作液中的两极间脉冲放电时产生的电蚀作用蚀除导电材料的特种加工方法,又称放电加工或电蚀加工,英文简称EDM。
按照工具电极的形式及其与工件之间相对运动的特征,可将电火花加工方式分为:利用轴向移动的金属丝作工具电极,工件按所需形状和尺寸作轨迹运动,以切割导电材料的电火花线切割加工;利用成型工具电极,相对工件作简单进给运动的电火花成形加工;利用金属丝或成形导电磨轮作工具电极,进行小孔磨削或成形磨削的电火花磨削;用于加工螺纹环规、螺纹塞规、齿轮等的电火花共轭回转加工;以及小孔加工、刻印、表面合金化、表面强化等其他种类的加工。
电火花加工时无切削力;不产生毛刺和刀痕沟纹等缺陷;工具电极材料无须比工件材料硬;直接使用电能加工,便于实现自动化;但是,加工后表面产生变质层,在某些应用中须进一步去除;而且,工作液的净化和加工中产生的烟雾污染处理比较麻烦。
电火花加工主要用于加工具有复杂形状的型孔和型腔的模具和零件;加工各种硬、脆材料,如硬质合金和淬火钢等;加工深细孔、异形孔、深槽、窄缝和切割薄片等;加工各种成形刀具、样板和螺纹环规等工具和量具。
1、电火花线切割机床
数控电火花线切割机床,如图0-10所示,是利用电火花原理,将工件与加工工具作为极性不同的两个电极,作为工具电极的金属丝(铜丝或钼丝)穿过工件,由计算机按预定的轨迹控制工件的运动,通过两电极间的放电蚀除材料来进行切割加工的一种新型机床。根据电极丝的运行速度,可分为低速走丝线切割机床和高速走丝线切割机床。低速走丝线切割机床走丝速度一般低于0.2m/s;高速走丝线切割机床走丝速度一般为8~10m/s。
图0-10 数控电火花线切割机床
2、电火花成型机床
数控电火花成型机床,如图0-11所示,在加工时,工具电极和工件分别接脉冲电源的两极,并浸入工作液中。通过间隙自动控制系统控制工具电极向工件进给,当两电极间的间隙达到一定距离时,两电极上施加的脉冲电压将工作液击穿,产生火花放电,在放电的微细通道中瞬时集中大量的热能,温度可高达一万摄氏度以上,压力也有急剧变化,从而使这一点工作表面局部微量的金属材料立刻熔化、气化,并爆炸式地飞溅到工作液中,迅速冷凝,形成固体的金属微粒,被工作液带走。这时在工件表面上便留下一个微小的凹坑痕迹,放电短暂停歇,两电极间工作液恢复绝缘状态。
在保持工具电极与工件之间恒定放电间隙的条件下,一边蚀除工件金属,一边使工具电极不断地向工件进给,最后便加工出与工具电极形状相对应的形状来。因此,只要改变工具电极的形状和工具电极与工件之间的相对运动方式,就能加工出各种复杂的型面。
图0-11 数控电火花成型机床
工具电极常用导电性良好、熔点较高、易加工的耐电蚀材料,如铜、石墨、铜钨合金和钼等。在加工过程中,工具电极也有损耗,但小于工件金属的蚀除量,甚至接近于无损耗。工作液作为放电介质,在加工过程中还起着冷却、排屑等作用。常用的工作液是粘度较低、闪点较高、性能稳定的介质,如煤油、去离子水和乳化液等。
第2章 实验注意事项与安全操作规程
实验是本课程教学中的一个重要环节,实验目的是为了使学生加强理论与实践相结合的能力,培养学生严肃认真和实事求是的工作作风和科学态度,锻炼在实践中分析问题和解决问题的聪明才智,激发努力开拓不断创新的精神。为使实验达到预期目的,特提出如下要求:
1. 实验室禁止吸烟,禁止酒后做实验。
2. 实验前认真预习实验指导书,明确实验目的和要求,理解实验内容,掌握实验步骤及注意事项。
3. 按实验指导书中的步骤和指导教师的要求做实验,认真作好实验记录。
4. 实验后应切断电源,把仪器、设备整理好,保持实验室清洁。
5. 按要求写实验报告,报告字迹要整齐,数据计算、图表、曲线均应符合要求。
为了按时完成实验,确保实验时人身安全与设备安全,要严格遵守如下规定的安全操作规程:
1. 严格遵守实验室安全操作规程及各项规章制度。
2. 实验前认真学习机床使用说明书。
3. 实验时,人体不可接触带电线路。
4. 接线或拆线都必须在切断电源的情况下进行。
5. 学生操作机床、运行程序前必须经指导教师检查和允许,并使组内其他同学引起注意后方可操作。实验中如发生事故,应立即按下“紧急停止”按钮,经查清问题和妥善处理故障后,才能继续进行实验。
6. 总电源或机床电源接通应由实验指导人员来控制,其他人只能由指导人员允许后方可操作,不得自行合闸。
7. 机床的使用必须严格遵守操作规程。操作时要耐心细致、轻拨缓旋,决不可养成盲目、随心所欲乱调仪器的不良习惯。和实验无关的仪器不得动用,也不得随意取用其他实验台上仪器设备。
8. 随时注意安全,当机床设备发生故障或事故时要立即停止实验,并报告指导老师。
9. 实验完毕后,必须清点仪器,摆放整齐,并作好清洁工作,经指导老师许可后才能离开。
10. 启动机床控制系统后应按照操作要求执行原点复归操作。
11. 运行程序前须认真检查,并由指导老师审查、确认。
12. 加工前,应进行程序预演和图形模拟。
手工编程篇
实验一 数控铣床操作与编程
一 、实验目的
1. 了解数控铣床的基本组成结构、基本运动、加工对象及其用途。
2. 掌握FANUC系统数控铣床的基本操作。
3. 掌握FANUC系统数控铣床程序编制。
二 、实验内容
1. 数控铣床的基本组成结构;
2. 数控铣床的基本运动坐标轴及其方向;
3. 数控铣床的加工对象及其用途;
4. 数控铣床操作面板各个功能键的作用;
5. FANUC系统数控铣床对刀方法;
6. FANUC系统数控铣床手工程序编制;
7. FANUC系统数控铣床简单零件的加工。
三 、实验设备
XK-714A型数控立式铣床、千分尺、刀具、试件
四 、实验步骤
1、 对照机床实物,参考图1-1,了解数控铣床的主要组成部件。
图1-1 数控铣床主要组成部件
2、 了解数控铣床各主要组成部件的结构、功能以及传动系统。
3、 了解数控铣床主要功能和加工对象
(1) 数控铣床主要功能:数控铣床配置不同,功能也不同,但以下主要功能基本都具备。
①. 直线插补: 完成数控铣削加工所应具备的基本功能之一,可分为平面直线插补、空间直线插补、逼近直线插补等。
②. 圆弧插补: 完成数控铣削加工所应具备的基本功能之一,可分为平面圆弧插补、逼近圆弧插补等。
③. 固定循环: 固定循环是指系统所作的固化的子程序,并通过各种参数适应不同的加工要求,主要用于实现一些具有典型性的需要多次重复的加工动作,如各种孔、内外螺纹、沟槽等的加工。使用固定循环可以有效地简化程序的编制。
④. 刀具补偿: 一般包括刀具半径补偿、刀具长度补偿、刀具空间位置补偿功能等。
⑤. 镜向、旋转、缩放、平移: 通过机床数控系统对加工程序进行上述处理,控制加工,从而简化程序编制。
⑥. 自动加减速控制: 该功能使机床在刀具改变运动方向时自动调整进给速度,保持正常而良好的加工状态,避免造成刀具变形、工件表面受损、加工过程速度不稳等情形。
⑦. 数据输入输出及 DNC 功能: 数控铣床一般通过 RS232C 接口进行数据的输入及输出,包括加工程序和机床参数等。当执行的加工程序超过存储空间时,就应当采用 DNC 加工,即外部计算机直接控制数控铣床进行加工。
⑧. 子程序功能: 对于需要多次重复的加工动作或加工区域,可以将其编成子程序,在主程序需要的时候调用它,并且可以实现子程序的多级嵌套,以简化程序的编写。
⑨. 自诊断功能: 自诊断是数控系统在运转中的自我诊断,它是数控系统的一项重要功能,对数控机床的维修具有重要的作用。
(2)数控铣床主要加工对象:
①. 平面类零件
加工面平行、垂直于水平面或与水平面成定角的零件称为平面类零件,这一类零件的特点是:加工单元面为平面或可展开成平面。其数控铣削相对比较简单,一般用两坐标联动就可以加工出来。
②. 曲面类零件
加工面为空间曲面的零件称为曲面类零件,其特点是加工面不能展开成平面,加工中铣刀与零件表面始终是点接触示。
③. 变斜角类零件
加工面与水平面的夹角呈连续变化的零件称为变斜角类零件,以飞机零部件常见。 其特点是加工面不能展开成平面,加工中加工面与铣刀周围接触的瞬间为一条直线。
④. 孔及螺纹
采用定尺寸刀具进行钻、扩、铰、镗及攻丝等,一般数控铣都有镗、钻、铰功能。
4、 数控铣床操作面板上各个按键的功用
数控铣床的操作面板由机床控制面板和数控系统操作面板两部分组成, 如图1-2所示。
(1) 数控系统操作面板
数控系统操作面板由显示屏和 MDI 键盘两部分组成,其中显示屏主要用来显示相关坐标位置、程序、图形、参数、诊断、报警等信息,而 MDI 键盘包括字母键、数值键以及功能按键等,可以进行程序、参数、机床指令的输入及系统功能的选择。详细介绍参见表1-1。
(2) 机床控制面板
机床控制面板上的各种功能键可执行简单的操作,直接控制机床的动作及加工过程,一般有急停、模式选择、轴向选择、切削进给速度调整、主轴转速调整、主轴的起停、程序调试功能及其它 M 、 S 、 T 功能等,其详细说明参见表1-2。
图1-2 FANUC控制系统面板
表1-1 CRT/MDI面板功能键
英文标识 |
按 键 |
用 途 说 明 |
POS 位置键 |
|
用于显示位置界面。在屏幕(CRT)上显示刀具现在位置,可以用机床坐标系、工件坐标系、增量坐标及刀具运动中距离指定位置剩余的移动量等四种不同的方式表示。 |
PROG 程序键 |
|
用于显示程序界面。在编辑方式下,编辑和显示在内存中的程序,可进行程序的编辑、检索及通信;在MDI方式,可输入和显示MDI数据,执行MDI输入的程序;在自动方式可显示运行的程序和指令值进行监控。 |
OFFSET SETTING 偏置/设置键 |
|
用于显示偏置/设置(SETTING)界面。刀具偏置量设置和宏程序变量的设置与显示;工件坐标系设定页面;刀具磨损补偿值设定页面等。 |
SYSTEM 系统键 |
|
用于显示系统界面。设定和显示运行参数表,这些参数供维修使用,一般禁止改动;显示自诊断数据。 |
MESSAGE 信息键 |
|
用于显示信息界面。按此键显示报警信息等。 |
CUSTOM GRAPH 图形显示键 |
|
用于显示宏程序界面和图形显示界面。 |
SHIFT 换档键 |
|
在该MDI键盘上有些键具有两个功能,按下SHIFT键可以在这两个功能之间进行切换,当一个键右下角的字母可被输入时,就会在屏幕上显示一个特殊的字符E。 |
CAN 取消键 |
|
按下此键,删除上一个输入的字符或字母。 |
INPUT 输入键 |
|
当按下一个字母键或者数字键时,再按该键,数据被输入到缓存区,并且显示在屏幕上,要将输入缓存区的数据拷贝到偏置寄存器,请按下这个键,它与软键上的[INPUT]键是等效的。 |
ALTER 替换键 |
|
编辑时在程序中光标指示位置替换字符。 |
INSERT 插入键 |
|
编辑时在程序中光标指示位置插入字符。 |
ALTER 替换键 |
|
编辑时在程序中光标指示位置替换字符。 |
PAGE 上翻页键 |
|
用于在屏幕上显示当前屏幕界面的前一页的界面 |
PAGE 上翻页键 |
|
用于在屏幕上显示当前屏幕界面的后一页的界面 |
HELP 帮助键 |
|
当对MDI键的操作不明白时,按下这个键可以获得帮助. |
RESET 复位键 |
|
用于解除报警.程序复位 |
CUROR 光标移动键 |
|
按下些键时,光标按箭头所示方向移动 |
5、 开机
打开外部电源开关,启动机床电源,将操作面板上的紧急停止按钮右旋弹起,按下操作面板上的电源开关,若开机成功,显示屏显示正常,无报警。机床回原点
6、 开机后的首要工作是回机床原点。
(1)检查坐标值,保证 X 、 Y 均在 -30 以下。若不符合要求,则选择手动操作模式,利用手轮将 X 、Y、 Z 的机械坐标值移动到符合要求为止。
(2)在回原点模式下,选中“ + ”键,再按住 X 键,将 X 轴回原点,回原点完成后,对应的指示灯闪烁,同理将Y、 Z 轴回原点。
7、 注意事项
回原点时必须先回Z 轴,再回X、Y轴,否则可能发生碰撞。
表1-2 机床控制面板功能键
按 钮 |
名 称 |
功 能 说 明 |
|
方式选择
|
编辑 |
旋钮打至该位置后,系统进入程序编辑状态。 |
自动 |
旋钮打至该位置后,系统进入自动加工模式。 |
MDI |
旋钮打至该位置后,系统进入MDI模式,手动输入并执行指令。 |
手动 |
旋钮打至该位置后,机床处于手动模式,连续移动。 |
手轮 |
旋钮打至该位置后,机床处于手轮控制模式 |
快速 |
旋钮打至该位置后,机床处于手动快速状态。 |
回零 |
旋钮打至该位置后,机床处于回零模式。 |
DNC |
旋钮打至该位置后,输入输出资料。 |
示教 |
旋钮打至该位置后,机床处于示教模式。 |
|
接通 |
接通电源。 |
|
|
断开 |
关电源。 |
|
|
循环启动 |
程序运行开始;系统处于“自动运行”或“MDI”位置时按下有效,其余模式下使用无效。 |
|
|
进给保持 |
程序运行暂停,在程序运行过程中,按下此按钮运行暂停。按“循环启动” 恢复运行。 |
|
|
跳步 |
此按钮被按下后,数控程序中的注释符号“/”有效。 |
|
|
单段 |
此按钮被按下后,运行程序时每次执行一条数控指令。 |
|
|
空运行 |
点击该按钮后系统进入空运行状态。 |
|
|
机床锁定 |
锁定机床。 |
|
|
选择停 |
此按钮被按下后,“M01”代码有效。 |
|
|
机床复位 |
复位机床。 |
|
|
急停按钮 |
按下急停按钮,使机床移动立即停止,并且所有的输出如主轴的转动等都会关闭。 |
|
|
X正方向按钮 |
点击该按钮,机床将向X轴正方向移动。 |
|
|
X负方向按钮 |
点击该按钮,机床将向X负方向移动。 |
|
|
Y正方向按钮 |
点击该按钮,机床将向Y正方向移动。 |
|
8、 程序的输入
程序的输入有多种形式,可通过手动数据输入方式( MDI )或通信接口将加工程序输入机床。
9、 程序调试
程序的调试是在数控铣床上运行该程序,根据机床的实际运动位置、动作以及机床的报警等来检查程序是否正确。一般可以采用以下方式:
(1) 机床的程序预演功能
程序输入完后,把机械运动、主轴运动以及 M 、 S 、 T 等辅助功能锁定,在自动循环模式下让数控铣床静态地执行程序,通过观察机床坐标位置数据和报警显示判断程序是否有语法、格式或数据错误。
(2) 抬刀运行程序
向 + Z 方向平移工件坐标系,在自动循环模式下运行程序,通过图形显示的刀具运动轨迹和坐标数据等判断程序是否正确。
10、 确定程序及加工参数正确无误后,选择自动加工模式,按下数控启动键运行程序,对工件进行自动加工。
(1) 程序运行方式
常见的程序运行方式有全自动循环、机床空运转循环、单段执行循环、跳段执行循环等。
(2) 注意事项
在程序运行时应注意以下问题:
①. 程序运行前要 做好加工准备,遵守安全操作规程,严格执行工艺规程;
②. 正确调用及执行加工程序;
③. 在程序运行过程中,适当调整主轴转速和进给速度,并注意监控加工状态,随时注意中断加工。
11、 程序执行完毕后,返回到设定高度,机床自动停止,松开夹具,卸下工件,用相应测量工具进行检测, 检查是否达到加工要求。
12、 数控铣削加工零件的检测,一般常规尺寸仍可使用普通的量具进行测量,如游标卡尺、内径百分表等,也可以采用投影仪测量;而高精度尺寸、空间位置尺寸、复杂轮廓和曲面的检验则只有采用三坐标测量机才能完成。
五、零件加工参数及参考程序
被加工零件如图1-3所示,工件厚度为20mm,φ50㎜的孔和工件的外轮廓已粗加工过,周边留了5㎜余量,要求精加工φ50㎜的孔和工件的外轮廓,单件生产,材料45#钢。
1、程序编制
(1) 确定工艺方案及工艺参数
以底面和φ50为定位基准,对刀点选在ф50孔的中心点上,加工刀具采用φ20的平底立铣刀,先加工φ50的孔后加工工件外轮廓,加工外轮廓路线顺序:按照ABCDEFGH线路进行铣削,加工工艺参数均为S200r/min,F50mm/min;
(2) 数学处理
建立工件坐标系,选φ50孔中心点为工件的坐标原点,Z的点为工件的上表面,在此坐标系中,A、B、C与G、H各点的坐标可从图纸中直接得到,其中D、E、F点的坐标计算结果如下:D(-37.707,35)、E(44.790,22.222)、F(80.623,0);
图1-3 零件简图
(3) 进刀方法及起刀点坐标
在工件BA线的延长线法向切入,故起刀点坐标为(-120,-60,100)。
(4) 编写程序
加工φ50孔的参考程序:
O0001
N10 G92 X0 Y0 Z100.0;
N20 G00 Z-22.0 S200 M03;
N30 G01 G41 X25.0 D01 F50 M08;
N40 G03 I -25.0;
N50 G00 G40 X0 Y0 M09;
N60 Z100.0;
N70 M30;
加工外轮廓的参考程序:
O0002;
N10 G92 X0 Y0 Z100.0;
N20 G00 X-120.0 Y-60.0 S200 M03;
N30 Z-22.0;
N40 G41 X-75.0 D01 F50 M08;
N50 G01 Y70.0;
N60 X55.0 Y90.0;
N70 X37.707;
N80 G02 X44.790 Y 22.222 R50.0;
N90 G03 X80.623 Y0 R40.0;
N100 G01 X105.0;
N110 X-55.0;
N120 Y-75.0;
N130 G00 G40 X-120.0 Y-60.0 M09;
N140 Z100.0;
N150 M30;
六 实验思考题
1. 简述数控铣床主要组成部件及其功能。
2. 简述数控铣床的主要功能及加工对象。
3. 列举数控铣床操作面板上常用功能键并加以解释。
4. 常用数控铣床坐标轴有哪些,方向如何?
5. 按照图1-4~1-6所示尺寸,编写数控加工程序,其它参数合理自定。
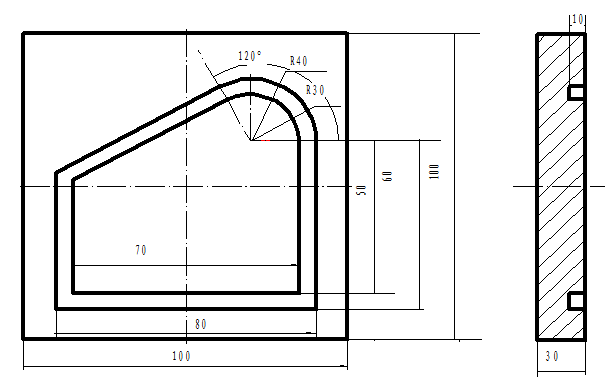
图1-4
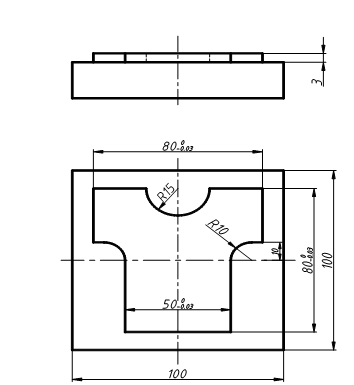
图1-5
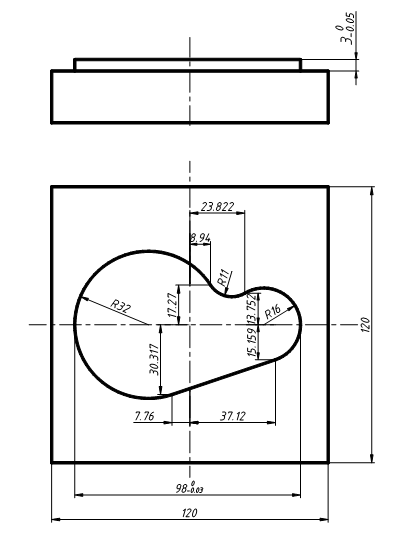
图1-6
实验二 加工中心操作与编程
一、实验目的
1. 了解加工中心的基本组成结构、基本运动、加工对象及其用途。
2. 掌握FANUC系统加工中心的基本操作。
3. 掌握FANUC系统加工中心程序编制。
二、实验内容
1. 加工中心的基本组成结构;
2. 加工中心的基本运动坐标轴及其方向。
3. 加工中心的加工对象及其用途。
4. 加工中心操作面板各个功能键的作用。
5. FANUC系统加工中心手工程序编制。
6. FANUC系统加工中心简单零件的加工。
三、实验设备
VB-825A FEELER型立式加工中心、千分尺、刀具、夹具、试件
四、实验步骤
1、 对照机床实物,参考图2-1,了解加工中心的主要组成部件。
图2-1 加工中心
2、 主要加工对象
加工中心是在数控铣床的基础上增加了刀库和自动换刀装置,适合加工复杂曲面、箱体类零件、异形件,以及盘、套、板类零件。
3、 加工中心操作面板上各个按键的功能
加工中心的操作面板由机床控制面板和数控系统操作面板两部分组成,与数控铣床的操作面板类似,具体参见表1-1和表1-2。
4、 加工指令
1) 自动返回参考点指令G28
执行G28指令,使各轴快速移动,分别经过指令的点返回到参考点定位。在使用G28指令时,必须先取消刀具半径补偿,而不必先取消刀具长度补偿,因为G28指令包含刀具长度补偿取消、主轴停止、切削液关闭等功能。故G28指令一般用于自动换刀。
程序格式: G91 G28 X0 Y0 Z0;
2) 换刀指令
程序格式: T — ;
M06 ;
3) 固定循环的指定
指令格式为:G17 G90(G91)G99(G98)G73(~G89)X—Y—Z—R—Q—P—F—K—;
式中:
(1)定位平面由G17、G18或G19决定,立式加工中心常用G17。以下指令均用G17说明。
(2)返回点平面选择指令G98、G99: 由G98、G99决定刀具在返回时达到的平面,G98指令返回到初始平面,G99指令返回R点平面
一般地,如果被加工的孔在一个平整的平面上,我们可以使用G99指令,因为G99模态下返回R点进行下一个孔的定位,而一般编程中R点非常靠近工件表面,这样可以缩短零件加工时间,但如果工件表面有高于被加工孔的凸台或筋时,使用G99时非常有可能使刀具和工件发生碰撞,这时,就应该 使用G98,使Z轴返回初始点后再进行下一个孔的定位,这样就比较安全。
(3)孔加工方式,主要指G73、G74,G76、G81~G89等,模态变量。
(4)孔位数据: X、Y为孔位置坐标(G17定位平面)。
(5)孔加工数据(模态变量)。
Z:在G90时,Z值为孔底的绝对坐标值,在G91时,Z是R平面到孔底的增量距离。从R平面到孔底是按F代码所指定的速度进给。
R:在G91时,R值为从初始平面到R点的增量距离;在G90时,R值为绝对坐标值,此段动作是快速进给的。
Q:在G73或G83方式中,规定每次加工的深度,以及在G87方式中规定移动值。Q值一律是无符号增量值
P:孔底暂停时间,用整数表示,以ms为单位
F:进给速度,mm/min,攻螺纹时为F=S×T,S为主轴转速,T为螺距。
(6)重复次数(非模态变量)。
K:K为0时,只存储数据,不加工孔。在G91方式下,可加工出等距孔。
若正在执行固定循环的过程中NC系统被复位,则孔加工模态、孔加工参数及重复次数K均被取消。
4) 高速深孔钻孔循环指令G73,
对于孔深大于5倍直径孔的加工由于是深孔加工,不利于排屑,故采用间断进给,每次进给深度为Q,最后一次进给深度≤Q,退刀量为d,直到孔底为止。
程序格式:G73 X—Y—Z—R—Q—F—K
式中XY为孔的位置,Z为孔底位置,R为参考平面位置,Q为每次加工的深度,d为排屑退刀量,由系统参数设定。其动作过程,如图2-2所示:
图2-2 G73循环指令动作过程
5) 深孔往复排屑钻孔循环指令G83。
程序格式:G83 X—Y—Z—R—Q—F—K一;
该循环用于深孔加工,孔加工动作如图所示,Q和d与G73循环中的含义。相同,与G73略有不同的是每次刀具间歇进给后,快速退回到R点平面,有利于深孔加工中的排屑。
6) 钻孔循环指令G81
G81用于一般的钻孔。
程序格式:G81 X—Y—Z—R—F—K一;
7) 精镗孔循环指令G76。
该循环用于镗削精密孔。
程序格式:G76X—Y—Z—R—Q—P—F—K—;
孔加工动作如图所示,Q表示刀具的移动量,移动方向由参数设定。在孔底,主轴在定向位置停止,切削刀具离开工件的被加工表面并返回,这样可以高精度、高效率地完成孔加工而不损伤工件表面。
其动作过程,如图2-3所示。
图2-3 G76循环指令动作过程
8) 攻左螺纹循环G74与攻右螺纹循环G84。
程序格式:G74(G84 )X_Y_Z_R_P_F_K_;
9) 取消固定循环G80
G80指令被执行以后,固定循环(G73、G74、G76、G81~G89)被该指令取消,R点和Z点的参数以及除F外的所有孔加工参数均被取消。另外01组的G代码也会起到同样的作用。
五、零件加工参数与参考程序
编制图2-4所示零件孔加工程序,工件坐标系的确定如图中箭头所示。



简单工序提示:钻孔(Ф35) 粗镗孔(Ф39.5) 精镗孔(Ф40) 钻孔(2-Ф13) 锪孔(2-Ф22)。
刀具及参数:T01 钻头(钻Ф35孔);T02 镗刀(粗镗Ф39.5孔);T03镗刀(精镗Ф40孔);T04 钻头(钻2-Ф13孔);T05 锪孔刀(锪2-Ф22孔)。
图2-4 被加工零件简图
参考程序
O0001;
G40G80G17;
G00G91G30Z0; (回换刀点且刀盘自动旋转至T01准备换刀的位置)
T01;(选择刀具T01)
M06;(换刀)
G00G90G54X0Y0Z50.0;
G43Z20.0H01S180M13;(刀具长度补偿)
G99G83Z-75.0R3.0Q4.0F40;(钻Ф35孔,刀具快速回归R点Z3.0,每次钻4mm)
G80G91G30G49Z0;(回换刀点且刀盘自动旋转至T02准备换刀的位置)
T02;
M06;
G00G90X0Y0Z50.0;
G43Z20.0H02S200M13;
G99G85Z-75.0R3.0F30;(粗镗Ф39.5孔,按进给速度刀具回归镗孔R点Z3.0)
G80G91G30G49Z0 T03;(回换刀点且刀盘自动旋转至T03准备换刀的位置)
M06;(换刀)
G00G90X0Y0Z50.0;
G43Z20.0H03S260M13;
G99G76Z-75.0R3.0Q0.1F20;(精镗Ф40孔,主轴定向停止刀具偏移0.1mm后快速回归镗孔R点Z3.0,以免刀划伤孔表面)
G80G91G30G49Z0 T04;
M06;
G00G90X-60.0;
G43Z2.0H04S400M13;
G98G73Z-75.0R-35.0Q4.0F40;(钻Ф13孔,刀具快速回归起始点Z2.0)
X60.0;(按上程序段参数钻另一Ф13的孔(注:循环没取消时在新位置有续效))
G80G91G30G49Z0 T05;
M06;
G00G90G54X60.0;
G43Z2.0H05S400M13;
G98G82Z-50.0R-35.0P100F25;(锪Ф22孔,在孔底暂停0.1秒(P值单位:1/1000秒)
X-60.0;(按上程序段参数锪另一Ф22的孔)
G80G91G28G49Z0;
M05;
G91G28Y0
M30;
六 实验思考题
1. 简述数控加工中心主要组成部件及其功能。
2. 简述数控加工中心的主要功能及加工对象。
3. 列举数控加工中心操作面板上常用功能键并加以解释。
4. 常用数控加工中心坐标轴有哪些?方向如何?
5. 按照图2-5所示尺寸,编写数控加工程序,其它参数合理自定。
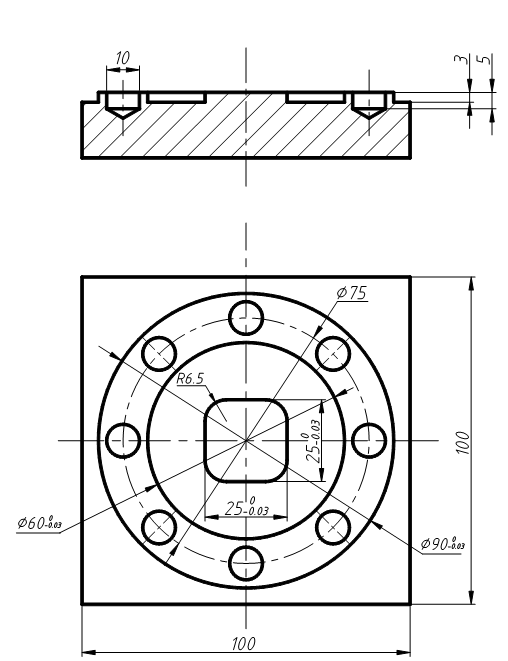
图2-5 零件图
实验三 数控车床操作与编程
一、实验目的
1. 了解数控车床的基本组成结构、基本运动、加工对象及其用途。
2. 了解数控车床与普通车床各自的特点;
3. 掌握FANUC系统简易数控车床的基本操作。
4. 掌握FANUC系统数控车床程序编制。
二、实验内容
1. 数控车床的基本组成结构;
2. 数控车床的基本运动坐标轴及其方向。
3. 数控车床的加工对象及其用途。
4. 数控车床和普通车床各自的特点。
5. 数控车床操作面板各个功能键的作用。
6. 数控车床对刀方法。
7. FANUC 0i-TB系统数控车床手工程序编制。
8. FANUC 0i-TB系统数控车床简单零件的加工。
三、实验设备
CKA6136和CKA6136i型卧式数控车床、普通车床、千分尺、刀具、试件
四、实验步骤
1、 对比数控车床和普通车床
与普通车床相比,数控车床具有以下特点:
(1) 采用了全封闭或半封闭防护装置:数控车床采用封闭防护装置可防止切屑或切削液飞出,给操作者带来意外伤害。
(2) 采用自动排屑装置:数控车床大都采用斜床身结构布局,排屑方便,便于采用自动排屑机。
(3) 主轴转速高,工件装夹安全可靠:数控车床大都采用了液压卡盘,夹紧力调整方便可靠,同时也降低了操作工人的劳动强度。
(4) 可自动换刀:数控车床采用了自动回转刀架,加工时可自动换刀,连续完成多道工序的加工。
(5) 主、进给传动分离:数控车床的主传动与进给传动采用了各自独立的伺服电机,使传动链变得简单、可靠,同时,各电机既可单独运动,也可实现多轴联动。
2、 数控车床主要组成结构
(1) 对照机床实物,参考图3-1和图3-2,了解数控车床的主要组成部件。
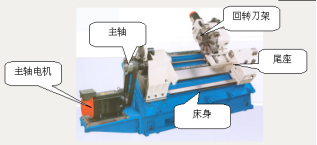
图3-1 车床外观主要部件 图3-2 车床内部主要组成部件
(2) 了解数控车床各主要组成部件的结构、功能以及传动系统。
3、 数控车床坐标系
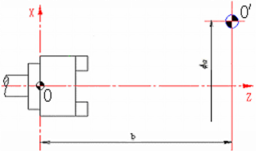
图3-3 数控车床坐标系
数控车床坐标系如图3-3所示。产生切削力的主轴轴线为Z轴,刀具远离工件的方向为正向;X轴位于平行工件装夹面的水平面内,垂直于工件回转轴线(Z轴),刀具远离工件的方向为正向。
4、 数控车床主要功能和加工对象
(1)不同数控车床其功能也不尽相同,各有特点,但都应具备以下主要功能。
①. 直线插补功能
控制刀具沿直线进行切削,在数控车床中利用该功能可加工圆柱面,圆锥面和倒角。
②. 圆弧插补功能
控制刀具沿圆弧进行切削,在数控车床中利用该功能可加工圆弧面和曲面。
③. 固定循环功能
固化了机床常用的一些功能,如粗加工、切螺纹、切槽、钻孔等,使用该功能简化了编程。
④. 恒线速度车削
通过控制主轴转速保持切削点处的切削速度恒定,可获得一致的加工表面。
⑤. 刀尖半径自动补偿功能
可对刀具运动轨迹进行半径补偿,具备该功能的机床在编程时可不考虑刀具半径,直接按零件轮廓进行编程,从而使编程变得方便简单。
(2)数控车床主要加工对象:
数控车床主要用于轴类或盘类零件的内外圆柱面、任意角度的内外圆锥面、复杂回转内外曲面和圆柱、圆锥螺纹等的切削加工,并能进行切槽、钻孔、扩孔、铰孔及镗孔等,特别适合加工形状复杂的零件。
5、 数控车床操作面板上各个按键的功能
数控车床的操作面板,如图3-4所示,由机床控制面板和数控系统操作面板两部分组成。
(1) 机床控制面板
机床控制面板上的各种功能键可执行简单的操作,直接控制机床的动作及加工过程,其功能详细说明可参见表3-1。
(2) 数控系统操作面板
由显示屏和 MDI 键盘两部分组成,其中显示屏主要用来显示相关坐标位置、程序、图形、参数、诊断、报警等信息; MDI 键盘包括字母键、数值键以及功能按键等,可以进行程序、参数、机床指令的输入及系统功能的选择。其功能详细说明可参见表1-1。
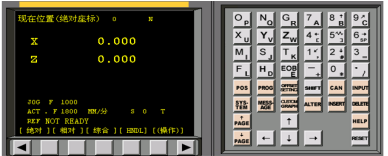
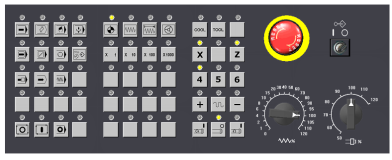
图3-4 数控车床操作面板
表3-1 机床控制面板功能键
按 钮 |
名 称 |
功 能 说 明 |
|
|
编辑 |
旋钮打至该位置后,系统进入程序编辑状态。 |
|
自动 |
旋钮打至该位置后,系统进入自动加工模式。 |
|
MDI |
旋钮打至该位置后,系统进入MDI模式,手动输入和编辑程序。 |
|
手动(JOG) |
旋钮打至该位置后,机床处于手动连续移动模式。 |
|
手轮 |
旋钮打至该位置后,机床处于手轮控制模式 |
|
回零 |
旋钮打至该位置后,机床处于回零模式。 |
|
DNC |
旋钮打至该位置后,将数控系统与电脑相连,输入输出资料。 |
|
增量 |
旋钮打至该位置后,按手动脉冲方式进给。 |
|
单段执行(SINGLE) |
运行程序时单段运行,每次执行一条数控指令。 |
|
|
程序编辑开关 |
置于“ON”位置,可以编辑程序。 |
|
|
主轴转速调节 |
调节主轴转速,调节范围从50~120%。 |
|
|
进给速度调节旋钮 |
调节进给速度,调节范围从0~120%。 |
|
|
急停按钮 |
按下急停按钮,使机床移动立即停止,并且所有的输出如主轴的转动等都会关闭。 |
|
6、 开机
(1)检查机床的润滑站,油面应在上、下油标线之间 ;
(2)合上总电源开关;
(3)打开机床电源开关并给控制系统上电;
(4)以顺时针方向转动紧急停止开关。
7、 机床回原点
开机后的首要工作是回机床原点。
(1)检查坐标值,保证 X 、 Y 均在 -30 以下。若不符合要求,则选择手动操作模式,利用手轮将 X 、 Z 的机械坐标值移动到符合要求为止。
(2)在回原点模式下,选中“ + ”键,再按住 X 键,将 X 轴回原点,回原点完成后,对应的指示灯闪烁,同理将 Z 轴回原点。注意: 回原点时必须先回 X 轴,再回 Z 轴,否则刀架可能与尾座发生碰撞。
8、 对刀
(1)对刀的高低; (2)分别对X和Z坐标值。
9、 程序的输入
在编辑模式下,将程序保护键钥匙转到“ OFF ”位置,即可进行程序的输入及编辑。如机床带有通信接口,也可从外部设备输入,并能直接执行外部程序。
10、 程序的调试
程序的调试一般可以采用以下方式:
(1) 机床程序预演
程序输入完以后,用手动把刀具从工件处移开,把机械运动、主轴运动以及 M 、 S 、 T 等辅助功能锁定,在自动循环模式下让程序空运行,通过观察机床坐标位置数据和报警显示判断程序是否有语法、格式或数据错误。
(2) 图形模拟加工
有图形模拟加工功能的数控车床,在自动加工前,为避免程序错误、刀具碰撞工件或卡盘,可对整个加工过程进行图形模拟加工,检查刀具轨迹是否正确。
数控车床的图形显示一般为二维坐标( XOZ 平面)显示。模拟加工操作主要有:先输入毛坯内、外径以及长度尺寸、比例系数,选择刀具,然后进行模拟加工显示。如有错误,进行修改,再模拟加工,直到正确为止。
11、 如程序无误,取消空运行及机械锁定,机床重新回零后,把刀架调整到合适的位置,进入自动模式,选择需执行的加工程序,关好拉门,调好快速进给率、切削进给率,打开切削液,按下启动键,即可加工零件。
常见程序运行方式有全自动循环、机床锁住循环、机床空运转循环、单段执行循环、跳段执行循环等。
(1) 全自动循环
全自动循环是指在自动加工状态下,机床可完成选定程序的执行。
(2) 机床锁住循环
机床锁住循环是指数控系统工作,显示屏动态显示机床运动情况,但不执行主轴、进给、换刀、冷却液等动作(有的机床仅锁住进给运动)。此功能主要用于全自动循环加工前的程序调试。
(3) 机床空运转循环
自动加工前,不将工件或刀具装上机床,进行机床空动转,以检查程序的正确性。空运转时的进给速度与程序无关,为系统设定值,不能用于加工零件。
(4) 单段执行循环
在自动加工试切时,出于安全考虑,可选择单段执行加工程序的功能。单段执行时,每按一次数控启动键,仅执行一个程序的动作或程序中的一个动作,可使加工程序逐段执行。
(5) 跳段执行循环
自动加工时,系统可跳过某些指定的程序段,称跳段执行。如在某程序段首加上“ / ”(如 /N0050 G01 ……),且面板上按下“跳段”开关,则在自动加工时,该程序段被跳过不执行;而当释放此开关 , “ / ”不起作用,该段程序被执行。
12、 取下工件,用相应测量工具进行检测,检查是否达到加工要求。
13、 加工完零件后,关闭机床的总开关,最后关闭总电源 。
五、 零件加工参数与参考程序
1、按图3-5所示尺寸编写该零件的加工程序(毛坯尺寸为:Ф116mm)。



工艺路线:循环粗车外圆 光端面 精车外形至尺寸(含倒角) 切槽 车螺纹。
循环粗车外圆参数:△d=6mm、e=2mm、△u=2mm、△w=4mm。
刀具:T01:粗车外圆车刀;T02:精车外圆车刀;T03:切刀,刀刃宽4mm;T04:螺纹刀。
图3-5 被加工零件
参考程序:
O0001; N180 G00 X116.0 Z89.0;
N10 T0101; N190 G70 P60 Q120; (精车)
N20 S260 M03; N200 G00 X150.0 Z125.0 T0200;
N30 G00 X116.0 Z89.0; N210 T0303 S200;
N40 G71 U6.0 R2.0; N220 G00 X62.0 Z50.0 M08;
N50 G71 P60 Q120 U4.0 W5.0 F25; N230 G01 X24.0 F60; (切槽)
N60 G00 X18.0 S300; N240 G04 X2.0;
N65 G01 X30.0 W-6.0 F20; N250 G00 X62.0 M09;
N70 Z50.0; N260 X150.0 Z125.0 T0300;
N80 X60.0; N270 T0404 S300;
N90 G02 X80.0 Z20.0 R60.0; N280 G00 X89.0 Z56.0; (车螺纹循环起点)
N100 G01 Z8.0; N290 G92 X29.1 Z4.0 F4;(第1次进刀0.9mm)
N110 X100.0 Z0; N300 X28.5; (第2次进刀0.6mm)
N120 X116.0; N310 X27.9; (第3次进刀0.6mm)
N130 G00 Z85.0; N320 X27.5; (第4次进刀0.4mm)
N135 X35.0; N330 X27.4; (第5次进刀0.1mm)
N140 G01 X0 F60; (光端面) N340 X150.0 Z125.0 T0400;
N150 G04 X2.0; (暂停2秒) N350 M30;
N160 G00 X150.0 Z125.0 T0100;
N170 T0202;
2、按图3-6所示尺寸编写该零件精加工程序。
参考程序
O0005;
T0101;
S200 M03;
G00 X26.0 Z80.0;
G01 X36.0(或U10.0) W-25.0(或Z55.0)F80;
Z30.0(或W-25.0);
X44.0(或U8.0);
G03 X60.0(或U16.0) W-8.0(或Z22.0) R8.0(K-8.0)
G01 Z0(或W-22.0);
G00 X80.0(或U20.0) Z110.0(或W110.0);
M30;
六 实验思考题
1. 简述数控车床主要组成部件及其功能;
2. 比较数控车床与普通车床,简述各自的异同点和优缺点。
3. 列举数控车床操作面板上常用功能键并加以解释。
4. 常用数控车床坐标轴有哪些,方向如何?
5. 用直径编程方法,根据零件尺寸,编写图3-7~3-10所示数控车削加工程序,加工尺寸如图所示,其它参数合理自定。要求解释各程序段的作用。
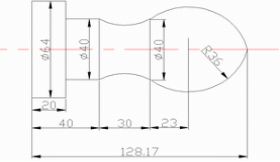
图3-7 图3-8
图3-9 图
3-10
6. 用固定循环指令加工如图3-11所示零件,试补充完成如下加工程序。
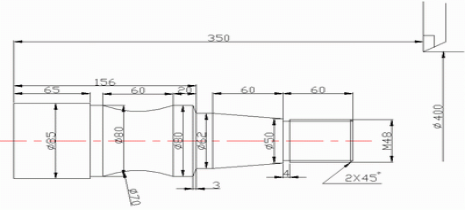
图3-11
加工程序
T0101;
M03 S1000;
G00 X60 Z2;
G73 U9.5 W0 R4;
___ P10 Q20 U1;
W0.5 F0.2;
_____ G00 X41.9 Z292 M08;
G01 X47.9 ____ F0.1;
Z227;
X50;
X62 W____;
Z155;
____;
X80 W-1;
W-19;
G02 _______ I63.25 K_____;
G01 Z65;
_____ X90;
G00 X200 Z350;
T0202;
M03 S315;
G00 X51 Z227;
G01 ____ F0.15;
G00 X51;
X200 Z350;
T0303;
G00 ____ ____;
G76 P01 2 60 Q0.1 R0.1;
____ X______ Z_____ P1.299 Q0.8 F______ ;
G00 X200 Z350 ;
M30;
实验四 数控电火花加工机床操作与编程
一、实验目的
1、了解数控电火花加工的原理、特点和应用。
2、了解数控电火花线切割机床的程序编制方法。
3、了解数控电火花加工机床的操作方法。
二、实验内容
1、讲解数控电火花加工机床的组成、原理、特点及应用。
2、演示数控电火花加工机床的加工过程。
3、通过上机操作,了解数控电火花线切割加工机床的零件加工过程。
三、实验设备
数控电火花线切割机床,数控电火花成型机床
四、数控电火花加工简介
1、电火花线加工的特点:
(1)由于脉冲放电的能量密度高,使其便于加工用普通的机械加工难于加工或无法加工的特殊材料和复杂形状的零件,并不受材料及热处理状况的影响。
(2)电火花加工时,工具电极与工件材料不接触,两者之间宏观作用力极小,工具电极不需要比加工材料硬,即可以柔克刚,故电极制造更容易。
2、电火花加工的应用:
电火花加工常用于模具的制造过程中,能加工各种高硬度、高强度、高韧性和高脆性的导电材料,如淬火钢、硬质合金等。加工时,钼丝与工件始终不接触,有0.01mm左右的间隙,几乎不存在切削力;能加工各种冲模、凸轮、样板等外形复杂的精密零件及窄缝等;尺寸精度可达0.02~0.01mm,表面粗糙度Ra值可达1.6μm。
3、实现电火花加工的条件
(1)工具电极和工件电极之间必须加以60V~300V的脉冲电压,同时还需维持合理的工作距离—放电间隙。大于放电间隙,介质不能被击穿,无法形成火花放电;小于放电间隙,会导致积炭,甚至发生电弧放电,无法继续加工。
(2)两极间必须放具有一定绝缘性能的液体介质。一般用煤油做为工作液。
(3)输送到两极间的脉冲能量应足够大。即放电通道要有很大的电流密度,一般为104~109A/cm2。
(4)放电必须是短时间的脉冲放电。一般放电时间为1μs~1ms。这样才能使放电产生的热量来不及扩散,从而把能量作用局限在很小的范围内,保持火花放电的冷极特性。
(5)脉冲放电需要多次进行,并且多次脉冲放电在时间上和空间上是分散的,避免发生局部烧伤。
(6)脉冲放电后的电蚀产物应能及时排放至放电间隙之外,使重复性放电能顺利进行。
4、数控电火花线切割加工原理
数控电火花线切割加工是电火花加工的一种。线切割加工是线电极电火花加工的简称,其基本原理如图4-1所示。被切割的工件作为工件电极,钼丝作为工具电极,脉冲电源发出一连串的脉冲电压,加到工件电极和工具电极上。钼丝与工件之间施加足够的具有一定绝缘性能的工作液。当钼丝与工件的距离小到一定程度时,在脉冲电压的作用下,工作液被击穿,在钼丝与工件之间形成瞬间放电通道,产生瞬时高温,使金属局部熔化甚至汽化而被蚀除下来。若工作台带动工件不断进给,就能切割出所需要的形状。由于贮丝筒带动钼丝交替作正、反向的高速移动,所以钼丝基本上不被蚀除,可使用较长的时间。线切割机床程序输入方法有三种:键盘输入,穿孔纸带输入和磁盘输入。
图4-1 线切割加工原理
5、数控电火花成型加工原理
数控电火花成型加工是电火花加工的一种,其基本原理如图4-2所示。
图4-2 数控电火花成型加工原理
被加工的工件做为工件电极,紫铜(或其它导电材料如石墨)做为工具电极。脉冲电源发出一连串的脉冲电压,加到工件电极和工具电极上,此时工具电极和工件均被淹没在具有一定绝缘性能的工作液(绝缘介质)中。在轴伺服系统的控制下,当工具电极与工件的距离小到一定程度时,在脉冲电压的作用下,两极间最近点处的工作液(绝缘介质)被击穿,工具电极与工件之间形成瞬时放电通道,产生瞬时高温,使金属局部熔化甚至汽化而被蚀除下来,使局部形成电蚀凹坑。这样以很高的频率连续不断地重复放电,工具电极不断向工件进给,就可以将工具电极的形状“复制”到工件上,加工出需要的型面。
五、数控电火花线切割机床的组成
数控线切割机床的外形如图4-3所示,其组成包括机床主机、脉冲电源和数控装置三大部分。
1、机床主机部分
机床主机部分由运丝机构、工作台、床身、工作液系统等组成。
(1)运丝机构:电动机通过联轴节带动贮丝筒交替作正、反向转动,钼丝整齐地排列在贮丝筒上,并经过丝架作往复高速移动。
(2)工作台:用于安装并带动工件在工作台平面内作X、Y两个方向的移动。工作台分上下两层,分别与X、Y向丝杠相连,由两个步进电机分别驱动。步进电机每接收到计算机发出的一个脉冲信号,其输出轴就旋转一个步距角,通过一对齿轮变速带动丝杠转动,从而使工作台在相应的方向上移动0.01mm。
图4-3 数控线切割机床示意图
(3)床身:用于支承和连接工作台、运丝机构、机床电器、及存放工作液系统。
(4)工作液系统:由工作液、工作液箱、工作液泵和循环导管组成。工作液起绝缘、排屑、冷却的作用。每次脉冲放电后,工件与钼丝之间必须迅速恢复绝缘状态,否则脉冲放电就会转变为稳定持续的电弧放电,影响加工质量。在加工过程中,工作液可把加工过程中产生的金属颗粒迅速从电极之间冲走,使加工顺利进行。工作液还可冷却受热的电极和工件,防止工件变形。
2、脉冲电源
脉冲电源又称高频电源,其作用是把普通的50Hz交流电转换成高频率的单向脉冲电压。加工时,钼丝接脉冲电源负极,工件接正极。
3、数控装置
数控装置以PC机为核心,配备有其他一些硬件及控制软件。加工程序可用键盘输入或磁盘输入。通过它可实现放大、缩小等多种功能的加工,其控制精度为±0.001mm,加工精度为±0.001mm。
六、数控电火花成型机床的组成
数控电火花成型机如图4-4所示,主要包括机床本体、脉冲电源、轴伺服系统(Z轴)、工作液的循环过滤系统和基于窗口的对话式软件操作系统等。
1、机床本体:床身、工作台、主轴箱等组成。
(1)床身:主要用于支承和连接工作台等部件,安放工作液箱等。
(2)工作台:用于安装夹具和工件,并带动工件在X、Y向作往复运动。
(3)主轴箱:用于装夹工具电极,并带动工具电极作Z向往复运动。
2、脉冲电源:其作用是把50Hz交流电转换成高频率的单向脉冲电流。加工时,工具电极接电源正极,工件电极接负极。
3、轴向伺服系统:其作用是控制Z轴的伺服运动。
4、工作液循环过滤系统:由工作液、工作液箱、工作液泵、滤芯和导管组成。工作液起绝缘、排屑、冷却和改善加工质量的作用。每次脉冲放电后,工件电极与工具电极之间必须迅速恢复绝缘状态,否则脉冲放电就会转变为持续的电弧放电,影响加工质量。在加工过程中,工作液可把加工过程中产生的金属颗粒迅速从电极之间冲走,使加工顺利进行。工作液还可冷却受热的电极和工件,防止工件变形。
图4-4 数控电火花成型机
5、基于窗口的对话式软件操作系统:使用本操作系统,工具电极可以方便地对工件进行感知和对中等操作,可以将工具电极和工件电极的各种参数输入并生成程序,可以动态观察加工过程中加工深度的变化情况,还可进行手动操作加工和文件管理等。
七、数控电火花线切割加工程序编制方法
1、程序格式
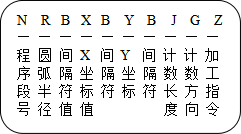
该程序格式称为“3B格式”。其中间隔符B的作用是将X、Y、J数码区分开。加工直线时,R为零。
在一个完整程序的最后应有停机符“FF”,表示程序结束。
(1)坐标系和坐标值X、Y的确定
平面坐标系是这样规定的:面对机床操作台,工作台平面为坐标平面,左右方向为X轴,且右方为正;前后方向为Y轴,且前方为正。
坐标系的原点随程序段的不同而变化:加工直线时,以该直线的起点为坐标系的原点,X、Y取该直线终点的坐标值;加工圆弧时,以该圆弧的圆心为坐标系的原点X、Y取该圆弧起点的坐标值。坐标值的负号均不写,单位为µm。
(2)计数方向G的确定
不管是加工直线还是圆弧,计数方向均按终点的位置来确定。具体确定的原则为:
加工直线时,计数方向取直线终点靠近的那一坐标轴。例如,在图4-5中,加工直线OA,计数方向取X轴,记作GX;加工OB,计数方向取Y轴,记作GY:加工OC,计数方向取X轴、Y轴均可,记作GX或GY。
加工圆弧时,终点靠近何轴,则计数方向取另一轴。例如:在图4-6中,加工圆弧AB,计数方向取X轴,记作GX;加工MN,计数方向取Y轴,记作GY;加工PQ,计数方向取X轴、Y轴均可,记作GX或GY。
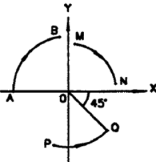
图4-5 直线计数方向的确定 图4-6 圆弧计数方向的确定
(3)计数长度J的确定
计数长度是在计数方向的基础上确定的,是被加工的直线或圆弧在计数方向的坐标轴上投影的绝对值总和,单位为µm。
例如,在图4-7中,加工直线OA,计数方向为X轴,计数长度为OB,数值等于A点的X坐标值。在图4-8中,加工半径为0.5mm的圆弧MN,计数方向为X轴,计数长度为500×3=1500µm,即MN中三段90º圆弧在X轴在投影的绝对值总和,而不是500×2=1000µm。
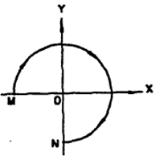
图4-7 直线计数长度的确定 图4-8 圆弧计数长度的确定
(4)加工指令Z的确定
加工直线时有四种加工指令:L1、L2、L3、L4。如图所示,当直线处于第I象限(包括X轴而不包括Y轴)时,加工指令记作L1;当处于第II象限(包括Y轴而不包括X轴)时,记作L2,L3,L4依此类推。
加工顺圆弧时有四种加工指令:SR1、SR2、SR3、SR4。如图所示,当圆弧的起点在第I象限(包括Y轴而不包括X轴)时,加工指令记作SR1;当起点在第II象限(包括X轴而不包Y轴)时,记作SR2;SR3、SR4依此类推。
加工逆圆弧时有四种加工指令:NR1、NR2、NR3、NR4。如图所示,当圆弧的起点在第I象限(包括X轴而不包括Y轴)时,加工指令记作NR1;当起点在第II象限(包括Y轴而不包括X轴)时,记作NR2;NR3、NR4依此类推。
2.编程方法
(1)确定加工路径起点。
(2)计算坐标值。按照坐标系和坐标X、Y的规定,分别计算坐标值。
(3)填写程序单,按程序标准格式逐段填写N、R、B、X、B、Y、B、J、G、Z。
八、实验步骤
1、介绍数控电火花加工的原理、特点和应用,使学生对数控电火花加工有初步了解。
2、讲授电火花加工的操作规范,使学生养成规范操作的习惯。
3、介绍数控电火花加工工艺过程及参数的选择原则。
(1)介绍工件的装夹与调整方法。
(2)介绍电极丝的选择原则和调整方法。
(3)介绍工艺参数的选择原则。
4、讲解电火花线切割机床的编程格式(3B编程格式)。
5、按图4-9,给出一段加工程序,演示由程序输入到程序执行的全过程。
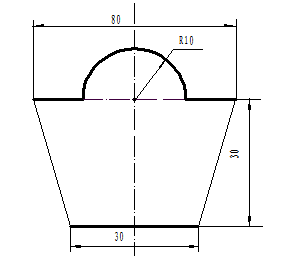
图4-9 被加工零件
编制加工程序(以圆弧圆心为坐标原点,起刀点在点(45,15)处):
N |
R |
B |
X |
B |
Y |
B |
J |
G |
Z |
1 |
0 |
|
45 |
|
0 |
|
15 |
Gy |
L4 |
2 |
0 |
|
10 |
|
0 |
|
30 |
Gx |
L3 |
3 |
10 |
|
0 |
|
0 |
|
20 |
Gy |
NR1 |
4 |
0 |
|
40 |
|
0 |
|
30 |
Gx |
L3 |
5 |
0 |
|
15 |
|
30 |
|
30 |
Gy |
L4 |
6 |
|
|
15 |
|
30 |
|
30 |
Gx |
L1 |
7 |
0 |
|
40 |
|
0 |
|
30 |
GY |
L1 |
8 |
0 |
|
45 |
|
0 |
|
5 |
Gx |
L1 |
FF |
九、思考题
1、简要说明电火花线切割加工原理。
2、简要说明数控电火花线切割机床与电火花成型机床的主要组成部件。
3、简要说明3B编程方法。
4、编制图4-10所示样板零件的数控电火花线切割加工程序。加工路线按照图中所标的①②……⑧进行。
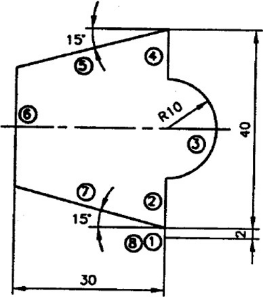
图4-10 样板零件
自动编程篇
实 验 五 使用Masterc am软件构建二维图形并生成NC程序
一 、实验目的
1、 掌握Master cam X系列软件的基本操作方法
2、 掌握Master cam X系列软件二维图形基本构建与编辑方法
3、 初步掌握Master cam X 生成轮廓铣NC程序方法
二 、实验内容
4、 练习Mastercam X系列软件基本操作命令
5、 练习Mastercam X 系列软件构建二维图形基本命令
6、 练习Mastercam X 生成轮廓铣NC程序
三 、实验设备
安装Mastercam X 系列软件的计算机
四 、实验步骤
1、 Mastercam基本操作
Mastercam是由美国CNC software公司开发的一套将CAD/CAM集成为一体的系统软件,分为Design、Mill、Lathe和Wire四大模块。以Mill为核心,包含了Design的3D建模功能,具有较强的CAM功能,它的主要特点是侧重于数控加工自动编程,简单易学,既能方便地绘制被加工零件图形,又能根据图形通过交互方式自动编制出数控加工程序。
Mastercam X4 软件主界面如图5-1所示,主要由标题栏、工具栏、下拉菜单、管理器窗口、绘图区及状态栏构成。下拉菜单主要功能、辅助功能和快捷键分别在表1、表2和表3中列出。
图5-1 Mastercam X4软件主界面
表1 下拉菜单功能表
下拉菜单 |
功 能 说 明 |
A分析 |
将绘图区中所选中的几何图形的坐标值和有关数据库信息显示在提示区中。例如有关点、线、弧、切线、曲线、曲面等几何要素和相关坐标尺寸等。 |
C绘图 |
在绘图区中制作各种几何图素,如点、线、弧、切线、曲线、曲面、倒角、文字等。 |
F档案 |
对图档进行存档、取档、档案转换或处理其它文件档,如NC、NCI、PST等。 |
M修整 |
用倒圆角、修剪延伸、打断、连接等指令修整几何图素。 |
X转换 |
用镜射、旋转、缩放和补正等指令转换已经存在的几何图素。 |
D删除 |
从屏幕上删除一个或一组几何图素,也可恢复已删除的图素。 |
S屏幕 |
设置系统规划参数、统计图素,改变屏幕显示特性:如开设多重视窗、视窗缩放、改变颜色、层别、属性等。 |
T刀具路径 |
用外形铣削、钻孔、挖槽、曲面加工、投影加工等指令产生刀具轨迹路径,进行刀具设定、工作设定及包括动态模拟刀具轨迹和后置处理的操作管理。 |
N公用管理 |
模拟刀具路径、修改NCI文件及后置处理生成NC加工程序等。 |
E离开系统 |
离开Mastercam系统 |
上层功能表 |
将主功能表返回上一层,也可按Esc 返回。 |
回主能表 |
将主功能表返回至根目录菜单。 |
表2 辅 助 功 能 表
辅助功能 |
功 能 说 明 |
Z |
设定当前构图平面深度,如构图面分别为俯视图(前视图、侧视图)时,该值分别表示Z轴(Y轴、X轴)的坐标值 |
颜色 |
设定当前系统的绘图颜色,最多可选用256种颜色 |
层别 |
设定当前绘图图层的某一层别,或关闭当前系统的某几个图层的显示层别。绘制较复杂的几何实体时,为避免某些几何数据的重复存放。或便于选中某几何图素,需把所绘制的几何实体的某些几何图素分别设置在几个图层中,并用多种颜色绘制 |
线型/线宽 |
设定当前绘图所用线型(如实线、虚线、中心线、假想线、折断线)和线的粗细。 |
刀具面 |
设定一个刀具面 |
构图面 |
设定一个绘图面 |
视角 |
设定屏幕所显示的图形视角 |
表3 Mastercam X4中快捷键
快捷键 |
对应功能 |
快捷键 |
对应功能 |
F1 |
视图放大 |
Alt+A |
自动存档 |
F2 |
模型缩小0.5倍 |
Alt+C |
运行C-Hooks程序 |
F3 |
刷新屏幕 |
Alt+D |
设置尺寸标注的参数 |
F4 |
分析图素的属性 |
Alt+E |
显示部分图素 |
F5 |
删除图素 |
Alt+G |
屏幕栅格设置 |
F9 |
显示当前坐标系 |
Alt+H |
获取帮助 |
Alt+F1 |
适合屏幕 |
Alt+O |
切换操作管理器 |
Alt+F4 |
退出Mastercam X |
Alt+P |
上一视角 |
Alt+F8 |
系统配置 |
Alt+S |
切换着色模式 |
Alt+F9 |
显示坐标轴 |
Alt+T |
切换显示刀具路径 |
Alt+1 |
俯视图 |
Alt+U |
返回上一步骤 |
Alt+2 |
前视图 |
Alt+V |
关于Mastercam X资料 |
Alt+3 |
后视图 |
Alt+X |
更改当前构图属性 |
Alt+4 |
底视图 |
Alt+Z |
打开层别管理器 |
Alt+5 |
右侧视图 |
Ctrl+A |
全选 |
Alt+6 |
左侧视图 |
Ctrl+C |
复制 |
Alt+7 |
等角视图 |
Ctrl+V |
粘贴 |
2、 利用Mastercam构建二维图形
利用Mastercam构建摇臂零件,零件简图如图5-2所示:
图5-2 摇臂零件简图
工件坐标原点选在Φ60的圆心上,先分别绘制图中Φ60和Φ30二个圆,其次将Φ30的圆平移到指定位置,然后分别绘制切线与切弧。具体操作过程:
(1) 绘制Φ60圆:下拉菜单一绘图一圆弧一圆心+点(或直接单击
) ,根据提示输入直径值“60”,然后根据提示“输入圆心点坐标”直接单击原点;
(2) 绘制Φ30圆:下拉菜单一绘图一圆弧一圆心+点(或直接单击
) ,根据提示输入直径值“30”,再根据提示“输入圆心点坐标”输入坐标(60,0),图形如图5-3所示;
(3)平移Φ30的圆:下拉菜单一转换一平移(或直接单击
),根据提示选择要平移的图素,单击图5-3中的P1点,弹出图5-4所示“平移”对话框,在直角坐标栏中输入平移坐标值(-160,-60),设定参数后单击
(确定)即可,图形如图5-5所示;
图5-3 绘制两个圆
图5-4 平移对话框
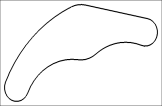
图5-5平移Φ30的圆 图5-6绘制切线与切弧 图5-7修剪后的图形
(4) 绘制切线:单击
,打开相切捕捉功能,下拉菜单一绘图一直线(或直接单击
),根据提示分别选取直线与图5-5中两圆大概的相切点P1与P2处即可;
④ 绘制切弧:用倒圆角功能绘制切弧比较简单,下拉菜单一绘图一倒圆角(或直接单击
),设置修整方式为N、S类型为标准及圆弧圆角半径值为“160”,然后单击图5-5中对应圆P2与P3点,并选取所需要的一段圆弧即可,设置圆角半径值为“60”,用同样的方法绘制另外两条切弧,图形如图5-6所示;
⑤ 图形修整:要求把图5-6非外轮廓的多余圆弧段修剪掉,修剪前需分别将三个圆打断,然后采用修剪单一物体与删除功能即可把多余的圆弧段修剪掉。下拉菜单一编辑一修剪/打断一两点打断(或直接点击)
,根据提示选择需打断的图素,可分别用鼠标捕捉图5-6圆的中点P1点与P2点为断点,在打断第三个圆选择断点时,因P3点为圆上的任意点,故需在抓点子菜单中,取消所有抓点设置后再单击该P3点,打断后可点击主功能表中的分析功能或工具条中的分析快捷功能键,检查被打断的图素是否真正被打断后再进行修剪。下拉菜单一编辑一修剪/打断一修剪/打断/延伸一修剪二物体(或直接单击
),根据提示选择需修剪的图素,单击需保留的线段处,如图5-6中P4点,然后在修整到某一图素的提示下,单击P5点即可修剪掉该多余圆弧段。其余圆弧段的修剪类同,修剪后的图形如图5-7所示。
3、 利用MasterCAM进行轮廓铣自动编程
图5-8 被加工零件简图
被加工零件简图如图5-8所示,其轮廓铣NC程序生成过程分三个步骤:
1) CAD过程
根据零件图纸计算机绘制被加工工件加工部位的几何图形,以产生图形文档。首先根据零件图特点确定如图5-8所示工件坐标系,然后绘制被加工工件加工部位的几何图形,其步骤如下:
(1)绘制矩形:下拉菜单一绘图一矩形(或直接点击
),在回应区提示下分别输入矩形左下角和右上角两点坐标值(0,-50)与(150,50);
② 绘制图形40×60的缺口:下拉菜单一绘图一任意线一绘制任意线(或直接单击
),单击水平线按钮
,用鼠标捕捉第一个端点后拖动鼠标至一定的位置,单击鼠标左键后,在回应区提示下输入y轴坐标值:“-20”,用相同的方法绘制另一条y=20的水平线和x=60的垂直线;
③ 倒四处R12的圆角下拉菜单一绘图一倒圆角,根据提示设置倒圆角半径R12、修剪等参数,并选择需倒圆角的图素;
④ 修剪图形,修剪前需打断矩形左边的直线:下拉菜单一编辑一修剪/打断一两点打断(或直接点击)
,根据提示选择需打断的图素,并用鼠标捕捉断点(中点)即可,下拉菜单一编辑一修剪/打断一修剪/打断/延伸一修剪二物体(或直接单击
),根据提示选择需修剪的图素,即用鼠标点击需保留的线段处即可。
2) CAM过程
CAM过程是在图形文档的基础上,输入工件切削加工参数,以产生刀具路径文档(NCI)。刀具路径文档是一种通用的刀具路径文档--刀具位置数据文档,刀具路径文档生成过程:主功能表一刀具路径一外形铣削(根据提示选择需加工的串连图素)一确定,屏幕中弹出如图5-9所示“刀具参数”对话框,根据被加工对象的加工工艺要求,选择所需要的刀具,并按图5-9所示参数填入,即主要包括进给率、主轴转速冷却液等;之后单击图中的“共同参数”选项,屏幕中弹出如图5-10所示外形参数对话框,主要包括安全与参考高度等,根据加工设备及加工要求,按图5-10所示填入相应的参数;最后分别单击切削参数、深度切削、进退刀参数和分层铣削等选项,输入相应参数值,按“确定”按钮后即可生成刀具路径文档,详情请参考教材,此处不再赘述。
图5-9 刀具参数对话框
图5-10 外形参数对话框
在主界面中如图5-11所示的“操作管理”对话框里,可分别选择操作管理表中的“刀路模拟”、“实体验证”及“后处理”等操作功能。刀具路径模拟如图5-12所示;实体切削验证(仿真加工)如图5-13所示。
在具有刀具补偿功能的数控系统的情况下,可按工件轮廓编程,图2-7中的“控制器补正位置”项可设置为“不补正”。 但为了在屏幕中便于观察刀具路径模拟与实体切削验证与实际加工一致,故该例是按刀具中心轨迹编程。
图5-11操作管理对话框
图5-12 刀具路径模拟
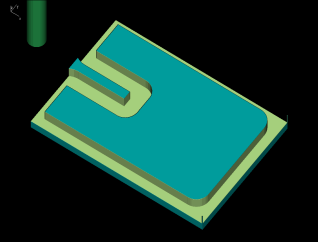
图5-13 实体仿真加工
3) 后(置)处理过程
执行后处理操作,系统将自动将NCI档案转化为CNC控制器(FANUC控制系统)可识别的NC加工程序(G代码),如图5-14所示。
图5-14由MasterCAM直接生成NC加工程序
生成的NC加工程序的前、后部分,往往需要根据机床控制系统特性与工厂习惯作进一步编辑修改。根据FANUC系统编程格式要求,图5-14所示NC加工程序,通过NC编辑器经手工修改后的NC加工程序如图5-15所示。
图5-15 经修改后的NC加工程序
五 实验思考题
1、 使用二维几何图形绘制方法分别绘制下列图形,并分别生成轮廓加工的刀具路径及数控加工程序。
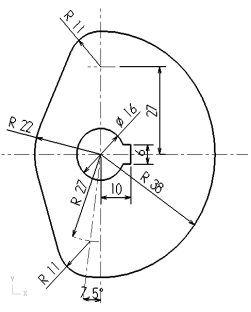
图5-8 梅花状图形 图5-9凸轮
2、 使用二维几何图形绘制方法绘制下列零件图,并分别生成轮廓加工的刀具路径及数控加工程序。
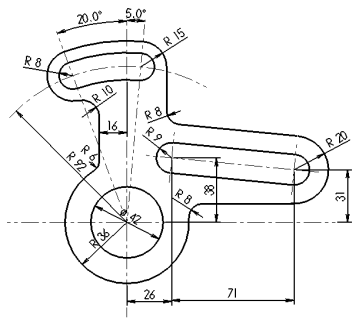
图5-10 零件图
实 验 六 使用Mastercam软件构建三维曲面图形
一 、实验目的
1、 进一步熟练掌握Mastercam X系列的基本操作
2、 掌握Mastercam X 三维曲面零件的构建与编辑方法
二 、实验内容
1、 掌握MastercamX 基本操作
2、 利用Mastercam X构建三维曲面零件
3、 利用Mastercam X编辑三维曲面零件
三 、实验设备
安装Mastercam X软件的计算机
四 、实验步骤
1、构建直纹曲面实例1
1) 构图方法
零件简图见图6-1,首先根据工件图纸特点选择工件坐标系原点,其次分别选择构图面(侧视图、前视图)及设定构图深度(Z值分别为:60、-60与0、60),绘制R25与R20四段圆弧,然后选择空间构图面,用直线分别连接四段圆弧,构成该直纹曲面线框,最后启动曲面功能绘制该直纹曲面。工件绝对坐标系原点选择如图6-1所示,即两个直纹曲面中心线相交点上。视角选择等角视图。
图6-1 直纹曲面
2)具体绘图过程
(1) 绘制圆柱直纹曲面两端圆弧:选择界面左下角2D/3D为2D,点击
中下拉箭头一选择
侧面绘图平面,Z深度:直接输入60,下拉菜单一绘图一圆弧(或直接单击
中下拉箭头)一极坐标圆弧;提示“请输入圆心点:单击原点;提示“输入半径值”:键盘输入“25”;提示“使用滑鼠指出起始角度的概略位置”:使用滑鼠点击相应位置;提示“使用滑鼠指出终止角度的概略位置”:使用滑鼠点击相应位置;键盘输入起始角度:180;键盘输入终止角度:0。单击
绘制完成。Z深度:(直接输入-60),用相同的方法绘制另一极坐标圆弧,图形如6-2所示。
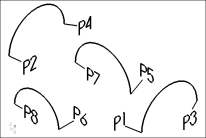
图6-2圆柱直纹曲面两端圆弧 图6-3圆锥直纹曲面两端圆弧
(2)绘制圆锥直纹曲面两端圆弧:选择界面左下角2D/3D为2D,点击
中下拉箭头一选择
前面绘图平面,,Z:(直接输入0),以①相同的方法分别绘制圆锥直纹曲面两端头两圆弧(注:R20的Z值为60),图形如6-3所示;
(3)绘制曲面线框:选择界面左下角2D/3D为3D;下拉菜单一绘图一任意线一绘制任意线(或直接单击
),提示“请指定端点”位置,分别用鼠标捕捉P1、P2;P3、P4;P5、P6;与P7、P8点即可,图形如图6-4所示;
(4)构造直纹曲面:先构造圆柱直纹曲面,下拉菜单一绘图一曲面一直纹曲面(提示“定义外形”)一单体(因为横切面外形线仅为单个圆弧,用鼠标分别捕捉P1与P2点)。
注:若用鼠标捕捉两圆弧的点不在对应位置,如用鼠标分别捕捉图6-2中的P1与P4点,将产生扭曲的曲面。
用相同的方法构造圆锥直纹曲面,图形如图6-5所示。实际上构造直纹曲面只需要绘制横切面的外形线即可,如图6-3所示。
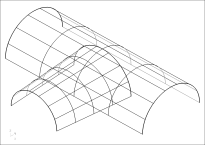
图6-4曲面框架 图6-5直纹曲面
(5) 图形存档:将图形存档。
2、构建直纹曲面实例2
1)构图方法
零件简图见图6-6,该零件的特点是R7.5直纹曲面与R10直纹曲面的中心线互相不垂直。R10直纹曲面的横切面外形线(2个R10的半圆形)可在侧视图中绘制,而R7.5直纹曲面横切面外形线(2个R7.5的半圆形)的绘制需建立一法线面,即在法线面中绘制R7.5两段圆弧。工件绝对坐标系原点选择如图6-6所
示。
图6-6 直纹曲面
图6-7 属性对话框
2)具体绘图过程
(1) 在俯视图中绘制R7.5与R10直纹曲面的中心线
① 单击界面下方属性按钮,弹出如图6-7所示的“属性”对话框,设定构图的线型为“中心线”;
② 在工具条中单击选择界面左下角2D/3D为2D,点击
中下拉箭头一选择
俯视图绘图平面,Z深度:直接输入0;
③ 下拉菜单一绘图一任意线一绘制任意线(或直接单击
)一单击水平线按钮
,提示“请指定第一个端点”一输入坐标点(15,0)后,向左拖动鼠标至大概的长度位置后单击鼠标左键,提示“请输入y轴坐标”,在水平线位置栏中输入“0”后按回车键;
④下拉菜单一绘图一任意线一绘制任意线(或直接单击
), 提示“请指定第一个端点”一单击原点,在角度栏中输入“-120”,在线长栏中输入“40”;之后延伸该中心线的右端至图6-8所要求的位置,即回下拉菜单一修剪/打断一修剪/打断/延伸,提示“选择图素去修剪或延伸”一单击该中心线右端,在线长栏中输入“5”后回车,图形如图6-8所示,将线型恢复为实线。
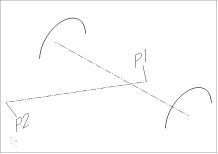
图6-8两直纹曲面的中心线 图6-9 R10直纹曲面两端圆弧
(2)绘制直纹曲面两端圆弧R10:选择界面左下角2D/3D为2D,设置视图面为等角视图,构图面为侧视图,Z值分别为“15”与“-40”,构图过程与图6-2相同,图形如图6-9所示;
(3)绘制直纹曲面两端圆弧R7.5
① 选择界面左下角2D/3D为2D,单击界面下方绘图平面与刀具面一法线定面(提示“请选择法线”,单击P2处)一选择视角;Z深度: 用鼠标捕捉P1点;
② 下拉菜单一绘图一圆弧(或直接单击
中下拉箭头)一极坐标圆弧;提示“请输入圆心点:单击原点;提示“输入半径值”:键盘输入“7.5”;提示“使用滑鼠指出起始角度的概略位置”:使用滑鼠点击相应位置;提示“使用滑鼠指出终止角度的概略位置”:使用滑鼠点击相应位置;键盘输入起始角度:180;键盘输入终止角度:0。单击
绘制完成。
③ Z深度: 用鼠标捕捉P2点;用相同的方法绘制另一极坐标圆弧,线框图形如图6-10所示。
(3)构造曲面:图形如图6-11所示。
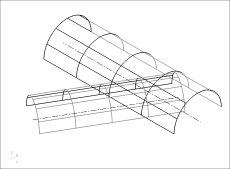
图6-10两直纹曲面框架 图6-11直纹曲面
五、 实验思考题
1、 利用下列左图线形框架,通过平面修正、牵引曲面和曲面倒圆角等功能构建右图所示洗手盆模型。
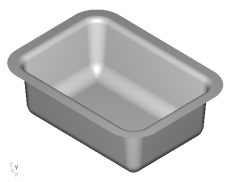
图6-12 洗手盆线形框架图 图6-13 洗手盆模型图
提示:底部倒圆角半径为R30。380X280平面与各牵引曲面倒圆角前,设置各牵引曲面的法向量朝外;380X280平面的法向量朝下,倒圆角半径为R12。
2、 绘制液化气灶旋钮曲面线形框架,如下面左图所示,并利用旋转曲面、扫描曲面、镜射与曲面倒圆角等功能构建右图所示液化气灶旋钮曲面。
提示:在前视图中分别绘制旋转曲线与旋转轴;在侧视图中分别绘制扫描曲线与扫描路径线。旋转曲面与扫描曲面生成后,利用“镜射”功能(对称Y轴)生成另一扫描曲面,最后曲面之间倒圆角(倒圆角半径为R1,修剪参数设置为“Y”),在曲面倒圆角之前,需将被倒圆角曲面的法向量设置朝内。
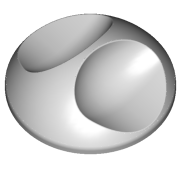
图 6-14液化气灶旋钮曲面线形框架图 图6-15 液化气灶旋钮曲面模型图
3、 分别在俯视图与前视图中绘制果汁杯曲面线形框架,如下面左图所示,并利用Coons曲面、举升曲面、扫描曲面与曲面倒圆角等功能构建如右图所示果汁杯曲面。
提示:Coons曲面由R110、R90、R28与半边椭圆四条曲线所构成,另一半通过对称X轴镜射而成;举升曲面是通过R7、R78组成的圆弧槽投影到两边Coons曲面上,再由该两Coons曲面上的投影曲线与R4、R78组成的圆弧槽所构成;Coons曲面与举升曲面之间倒圆角之前,设置Coons曲面的法向量朝内,举升曲面的法向量朝外(倒圆角半径为R2,修剪参数设置为“Y”)。
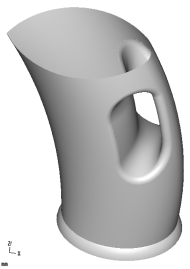
图6-16 果汁杯曲面线形框架图 图6-17果汁杯曲面模型图
实 验 七 使用Mastercam软件构建三维实体图形
一 、实验目的
掌握Mastercam X系列软件实体造型基本操作
二 、实验内容
利用挤出、旋转、扫描、布尔运算(交、并、差)等方法进行实体造型
三 、实验设备
安装Mastercam X系列软件的计算机
四 、实验步骤
1、 利用闭式串连曲线生成实体
1)构图方法:利用图7-1闭式串连曲线,挤出图7-2所示实体。
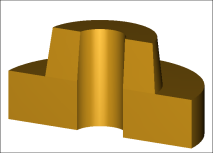
图7-1闭式串连曲线 图7-2 实体
图7-3 挤出主体参数设定 图7-4 挤出主体
2)具体绘图过程
(1)挤出主体:下拉菜单一实体一挤出实体,提示“选取挤出之串连图素1”,根据提示单击R50的圆弧,系数隐含为串连方式)一确定,根据屏幕中的箭头提示选择挤出方向(向上,可通过菜单中的反向改变方向)一确定,屏幕中弹出如图7.3所示参数设定对话框,其中包括“产生主体”、“切割主体”、“增加凸缘”、“拨模”及“挤出距离”等,根据实体要求进行选择或设置。第一次挤出时是实体的主体,只能选择“产生主体”,设置挤出距离为“30”,单击“确定”后图形如图7.4所示。
(2)挤出凸台:下拉菜单一实体一挤出实体,提示“选取挤出之串连图素1”,根据提示单击R30的圆弧)一执行,根据箭头提示选择挤出方向(向上)一确定,当屏幕中弹出如图7-5所示参数设定表时,按图7-5所示参数设定,即选择“增加拨模角”及角度为“5”、设置挤出距离为“30”、“增加凸缘”(即在主体上增加凸台,构成一个整体。否则挤出的为另一个主体),单击“确定”后图形如图7-6所示;
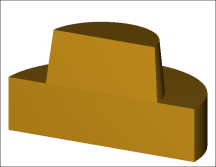
图7-5 挤出凸台参数设定 图7-6 挤出凸台
(3)切割主体: 下拉菜单一实体一挤出实体,提示“选取挤出之串连图素1”,根据提示单击R12.5的圆弧)一确定,根据箭头提示选择挤出方向(向下)一确定,当屏幕中弹出如图7-7所示参数设定表时,需挤出实体中的孔,故应选择“切割主体”,去掉“增加拨模角”,指定挤出长度≥“60”,单击“确定”即可,图形如图7.2所示。
注:在图6.5参数挤出之距离/方向栏中,另有一项指定挤出长度的选择方式,即延伸至指定点,在不便估计挤出长度的情况下非常有用。如上述用R12.5的圆弧“切割主体”挤出实体中的孔,不指定延伸距离,而指定延伸至指定点,当单击“确定”后,系统会提示请指定延伸点,然后用鼠标捕捉所需要的点即可,如此处可捕捉R50圆弧的中点。
图7-7 切割实体参数设定
2、 扫描实体
1)构图方法:利用图7-8闭式串连曲线及扫描线构成扫描实体。
2)绘图过程
下拉菜单一实体一扫描实体,提示“请选择要扫掠的串连图素1”,根据提示单击图7-8所示的圆)一确定;提示“请选择扫掠路径的串连图素”,根据提示单击图7-8所示的扫描线一确定,在屏幕中弹出的“扫掠实体之参数设定”表中选择“产生主体”后单击“确定”即可,实体如图7-9所示。
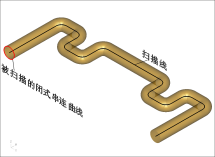
图7-8闭式串连曲线及扫描线 图7-9 扫描实体
注:实体举升与实体扫描的串连曲线必须是闭式的“面域”。
3、 泵盖零件实体
1)构图方法:泵盖零件。该零件是通过两个不同平面的四个闭式串连曲线挤出的实体,如图7-10所示。
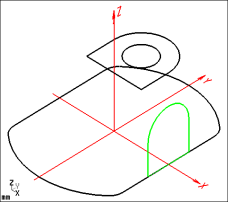
图7-10 泵盖零件 图7-11串连曲线(面域)
2)具体绘图过程:
(1) 根据零件图尺寸要求分别在俯视图上(Z深度=0 、Z深度=35)与侧视图上(Z深度=40)构图面构造串连封闭曲线)图,注意侧视图中拱形图形的封闭,如图7-11所示;
(2)利用图7-11串连闭式曲线,分别拉伸实体(Φ20的孔暂不拉伸,因为影响到下步实体边缘全部倒圆角,而孔两端是倒直角),如图7-12所示;
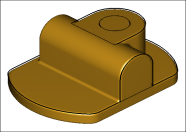
图7-12 拉伸 图7-13 倒圆角
(3)实体边缘全部倒圆角(R2),如图7-13所示;
(4)拉伸Φ20的孔(切割主体)并倒角(2×45°),其结果如图7-10所示。
五、 实验思考题
1、 分别在前视图与俯视图中绘制果冻盒线形框架,如下面左图所示,并利用旋转实体、实体扫描及旋转(旋转圆柱实体7次)、实体布尔差运算、实体倒圆角和实体抽壳等功能产生如下面右图所示果冻盒实体。
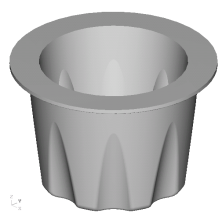
图7-14果冻盒线形框架图 图7-15 果冻盒实体模型图
实 验 八 三维曲面/实体零件NC程序生成
一 、实验目的
掌握Mastercam X 系列软件NC加工程序生成方法
二 、实验内容
使用Mastercam数控加工模块,设置加工路径,并生成NC代码。
三 、实验设备
安装Mastercam X系列软件的计算机
四 、实验步骤
1、零件的粗加工、精加工与多轴加工
针对不同曲面/实体的特点,Mastercam在不同的加工类型中各分多种加工方式,如图8-1、图8-2与图8-3所示。由图8-1与图8-2可知,粗加工与精加工之中有些加工方式是相同的。
图8-13 粗加工方式 图8-2精加工方式 图8-3多轴加工方式
1)粗加工
粗加工是从被加工零件表面上尽可能多地切掉多余材料,一般情况下是分层切削。
(1)平行铣削(含精加工)
可沿着特定方向(与X轴的特定夹角)生成一系列平行的刀具路径,通常加工单一的凸、凹体工件。
(2)放射状加工(含精加工)
一般是沿圆形工件的中心生成放射状径向刀具路径,故常用于加工圆形工件。
(3)投影加工(含精加工)
是将己生成的刀具路径或几何图形投影到所选取的曲面上生成刀具路径,通常用于雕刻加工中,如曲面上需雕刻花纹。
(4)曲面流线加工(含精加工)
是沿曲面流线方向生成刀具路径,通常用于不规则曲面,如Coons曲面的加工。
(5)等高外形(含精加工)
沿着曲面的外形以等高线(高度相同)的形式生成刀具路径,适用于加工余量基本一致、形状较接近零件的毛坯,如铸造件的加工。
(6)曲面挖槽粗加工
类似于二维零件中的挖槽加工,主要适用于切除封闭轮廓曲线所包围凹形工件材料的粗加工。
(7)钻削式加工
一种类似于钻孔的加工方法,依曲面形状在Z方向下降生成粗加工刀具路径,该加工方式可有效地避免刀具径向折断。
2)精加工
精加工是在粗加工的基础上尽可能地达到零件加工要求或最终加工要求的半精加工或最终加工。
(1) 环绕等距精加工
按被加工表面的轮廓产生等距离(等步距)环绕的精加工刀具路径,且刀具路径总是接触被加工曲面。
(2)交线清角
清除曲面交线处因刀具选择过大等原因残留材料的局部精加工。
(3)残料清角
清除因刀具选择过大或加工方式选择不当而残留在零件表面材料的局部精加工。
(4)陡斜面加工
清除粗加工时残留在曲面斜坡上材料的局部精加工。
(5)浅平面加工
清除粗加工时曲面浅面部分残留下来的一层薄薄材料的局部精加工,浅面面积由两斜坡角度确定,即角度越小则面积越大。
2、 利用平行铣削、交线清角加工方法零件进行加工
图8-4 零件图
1)工艺分析
已知该零件的材料为40Cr,该零件主要加工表面为平行于X轴,故釆用平行铣削分别进行粗加工与精加工,最后釆用交线清角加工方法进行局部精加工,以清除圆柱曲面、圆锥曲面与平面交线处残留材料。
2)制定工艺参数
(1)粗加工工艺参数选择:选择Φ16球头立铣刀,Z方向进给率5mm/分,X与Y方向(切削方向)的进给率40mm/分,主轴转速为400转/分,加工时冷却液开,见图8-5所示;给精加工预留量为0.5mm,安全高度等参数参见图8-6;Z方向分层切削,每次进刀量为2mm,切削方向误差值为0.05mm(误差值越小,刀具的步距就越小),最大切削间距为6mm(刀具的行距),见图8-7所示。
注:步距与行距越小,精度就越高,但加工程序的行数就越多。
(2)平行铣削精加工工艺参数选择:选择Φ10球头立铣刀,Z方向进给率3mm/分,X与Y方向的进给率30mm/分,主轴转速为800转/分,加工时冷却液开;切削方向误差值为0.01mm,最大切削间距为1.2mm。
(3)交线清角精加工工艺参数选择:选择Φ6球头立铣刀,Z方向进给率1mm/分,X与Y方向的进给率20mm/分,主轴转速为1200转/分,加工时冷却液开;切削方向误差值为0.005mm。
3)刀具轨迹的生成
(1)平行铣削粗加工刀心轨迹的生成:下拉菜单—刀具路径—曲面粗加工—平行铣削—凸(根据提示选择要加工的曲面:所有的—曲面)—确定,屏幕中弹出粗加工平行铣削参数选择对话框,按图8-5、图8-6与图8-7所示参数分别填入,点击“确定”按钮后,单击执行即可生成平行铣削粗加工刀心轨迹,粗加工效果如图8-8所示。
图8-5 粗加工刀具参数
图8-6 粗加工曲面加工参数
图8-7 平行铣削粗加工参数
图8-8 粗加工效果图
(2)平行铣削精加工刀心轨迹的生成:下拉菜单—刀具路径—曲面精加工—平行铣削,根据提示选择要加工的曲面—确定,屏幕中弹出平行铣削精加工参数选择对话框,如图8-9所示,根据前面 “制定工艺参数”中预先制定的内容,分别输入刀具参数、曲面加工参数与平行铣削精加工参数,单击确定即可生成如图8-10所示的平行铣削精加工刀具轨迹。
图8-9 平行铣削精加工参数
图8-10 平行铣削精加工刀心轨迹
(3)交线清角精加工刀心轨迹的生成:下拉菜单—刀具路径—曲面精加工—交线清角加工,根据提示选择要加工的曲面—确定,屏幕中弹出交线清角精加工参数选择对话框,如图8-11所示,根据前面 “制定工艺参数”中预先制定的内容,分别输入刀具参数、曲面加工参数与交线清角加工参数,单击确定即可生成交线清角精加工刀心轨迹,最终加工效果如图8-12所示。
图8-11 残料清角加工参数
图8-12 精加工效果图
最后调用系统后处理程序,即可生成整个零件数控加工特定数控机床的加工程序。
五、 实验思考题
1、参照图8-13和图8-14,分别构建下图所示凸、凹模图形,并分别生成粗、精加工的刀具路径及数控加工程序。
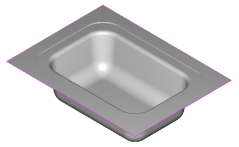
图8-13 洗手盆凸模模型图 图8-14洗手盆凹模模型图
3、 参照图8-15和8-16,分别构建下图所示凸、凹模图形,并分别生成粗、精加工的刀具路径及数控加工程序。

图8-15液化气灶旋钮凸模模型图 图8-16液化气灶旋钮凹模模型图
实 验 九 三维曲面/实体零件数控在线加工
一 、实验目的
综合应用Mastercam造型与NC加工知识、数控机床操作知识以及DNC加工知识,对零件进行造型与在线加工
二 、实验内容
1、 利用Mastercam对零件进行造型设计,并生成NC代码;
2、 进一步熟悉数控机床操作,尤其是DNC加工操作;
3、 熟悉DNC传输软件;
4、 DNC加工;
5、 测量加工好的零件,必要时使用高精度三坐标测量机;
三 、实验设备
安装Mastercam X系列软件的计算机、数控机床、三坐标测量机、量具、试件
四 、实验步骤
1、 使用Mastercam X软件绘出图9-1所示零件
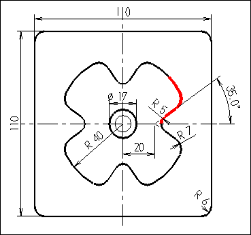
图9-1 零件图
工件坐标原点选在Φ17的圆心上,由图9-1可知,该图关键是梅花状图形的绘制,可先绘制图9-1粗实线所示部分,然后通过几何图形的转换,即镜射(对称45°线)与旋转(旋转三次,旋转角度90°)便可。具体操作过程略。
2、 刀具参数设定
从图形文档文件夹中调出梅花状零件图形文档后,下拉菜单一刀具路径一外形铣削,根据提示选择梅花状零件图形外形的串连图素一确定,屏幕中弹出外形铣削参数对话框,单击刀具项,如图9-2所示。在图空白处单击鼠标右键,屏幕中弹出如图9-3所示刀具形成对话框,点击“从刀具库中选取刀具”,屏幕中弹出选择刀具对话框,拖动移动条选择所需要的刀具。
图9-2 刀具参数对话框
图9-3 选择刀具对话框
中有中心钻、钻头、平刀、球刀、圆角刀、右牙刀等多种类型的刀具,根据该工序加工情况,选用Φ16的平刀,即平底立铣刀,之后单击“确定”按钮。用鼠标右键单击空白处所添加刀具的图形,屏幕中弹出图9-4所示定义刀具对话框,可对刀具进行编辑修改,但在具有刀具补偿功能的数控系统的情况下,由于是按工件轮廓编程,故无须对刀具进行修改。设定主轴转速、进给率等其它参数,从而完成了该加工工序的刀具参数设定。
图9-4定义刀具对话框
3、 加工参数设定
1. 外形铣削加工参数设定
点击外形铣削参数对话框中共同参数项,屏幕中弹出外形铣削参数表,共同参数按图9-5所示设定。
图9-5 外形铣削共同参数设定
4、 腔槽加工参数设定
操作过程为下拉菜单一刀具路径一标准挖槽,根据提示“选择串连图素1”,单击零件图中Φ17的圆;根据提示“选择串连图素2”,单击图中梅花状图形一确定,屏幕中弹出挖槽参数表,单击刀具参数项,根据加工要求,选择所需要的刀具(选择Φ12平底键槽刀),并填入相应的参数之后,单击共同参数项,弹出图9-6所示。共同参数设定后,单击粗铣/精修参数项,屏幕中弹出如图9-7所示粗铣/精修参数表,表中提供了多种加工切削方式可供选择,根据该零件腔槽边界线大部分是圆形的特点,选择“等距环切”方式挖槽,其它参数按图所示挖槽共同参数设定对话框。
图9-6挖槽共同参数设定对话框
图9-7 腔槽加工切削方式及有关参数选择
5、刀心轨迹仿真加工
外形铣削参数设定后,单击确定按钮后可生成外形铣削刀心轨迹文档;设定挖槽参数后,单击确定按钮后便可生成挖槽刀具路径文档。可分别在主界面上如图9-8所示操作管理对话框中分别点击刀具路径模拟、实体验证或后处理项,刀具路径模拟、实体验证如图9-9所示。
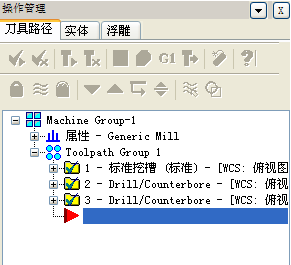
图9-8 操作管理对话框
。
刀具路径模拟
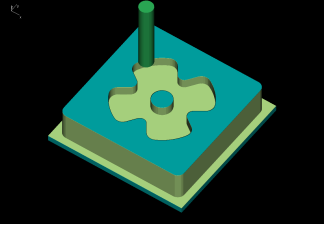
图9-9 腔槽实体加工仿真
6、后处理程序选择及数控加工程序的生成
在操作管理对话框中单击
,屏幕中弹出后处理对话框。单击更改后处理程式,屏幕中弹出如图9-10所示不同数控机床的后处理程序的对话框,系统隐含的是日本FANUC数控系统的后处理程序一一“Mpfan.pst”,若需其它数控机床的后处理程序,可在图中选择。
图9-10不同数控机床的后处理程序名
选择好后处理程序后单击图中的Run,屏幕中弹出是否要建立NCI文档询问框,单击是,系数将以图档文档名、以NCI为后缀名自动存入系数NCI文件夹中,为特定数控机床建立NC加工程序,接着屏幕中自动弹出保存NC加工程序的路径,输入NC加工程序名或默认系统以图形文档名保存后,屏幕中弹出该零件加工程序清单(利用程序文件编辑器对加工程序的首尾进行了必要的编辑)。
下图是该零件的部分NC加工程序清单(因篇幅关系删除了中间部分),其中N100至N138是该零件的外形铣削加工程序;N142至N344是该零件的挖槽加工程序。
NC加工程序清单
7、给机床通电,并执行原点复归。
8、安装好刀具、工件。
9、对刀;(注意图形的原点与工件原点一致)
10、做好数控设备的接收准备工作;
11、传输加工:(以VB-825A FEELER型数控立式加工中心为例)
(1) CNC机床选择“资料输入”模式;
(2) 按“程序启动”键,屏幕上出现“标头SKP”字样;
(3) PC机V24软件中选择“SEND”后回车,再选择一个要传输的程序文件,回车即OK!
12、零件质量检验分析;
13、做好设备的清洁工作。
五、实验思考题
1、 简述DNC加工的操作过程。
2、 对下列图形进行DNC加工
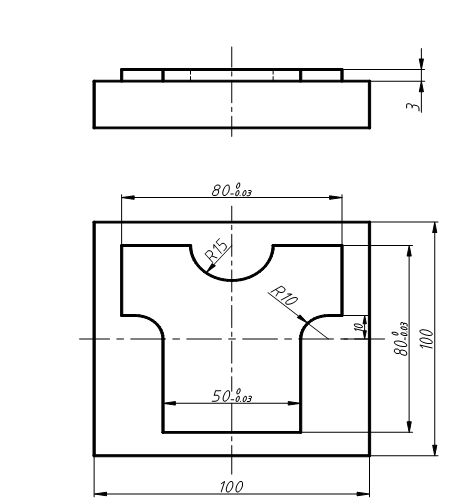
参 考 文 献
[1] 聂秋根,陈光明等编著. 数控加工技术. 高等教育出版社 ,2012
[2] 张超英、谢富春编著. 数控编程技术. 化学工业出版社,2004
[3] 张洪兴,聂秋根等编著. 数控机床编程•操作•维修. 航空工业出版社,2000
[4] 廖效果主编.数字控制机床.武汉:华中理工大学出版社,1999
[5] 周德俭主编.数控技术.重庆:重庆大学出版社, 2001
[6] 陈富安主编.数控机床原理与编程.西安:西安电子科技大学出版社, 2004
[7] 陈志雄主编.数控机床与数控编程技术.北京:电子工业出版社, 2003
[8] 刘战术,窦凯主编.数控机床及其维护.北京:人民邮电出版社, 2004
[9] 王爱玲主编. 现代数控原理及控制系统. 北京: 国防工业出版社, 2005
[10] 董瑞杰、黄一呜编著,最新Mastercam 7模具设计教程,中国石化出版社,2000;
[11] 蔡汉明、宋晓梅编著,数控编程—Mastercam 8.0实用教程,人民邮电出版社,2001;
[12] 严烈编著,Mastercam 9应用基础教程,冶金工业出版社,2003;
[13] 何满才编著,三维造型设计—Mastercam 9.0实例详解,人民邮电出版社,2003;
[14] 何满才编著,模具设计与加工—Mastercam 9.0实例详解,人民邮电出版社,2003;
[15] 王卫兵主编,数控编程100例,机械工业出版社,2004。
附录
实 验 报 告
实 验 一
学院实验报告
班级 学号 姓名
实验课程:
实验项目: 数控铣床编程与操作
实验日期: 年 月 日
预 习 简 要 |
|
实 验 目 的 |
|
实 验 设 备 |
|
实 验 内 容 |
|
零 件 图 |
|
数 控 加 工 程 序 |
|
实 验 步 骤 |
|
实 验 结 果 分 析 思 考 和 心 得 |
|
教师签名: |
实 验 二
学院实验报告
班级 学号 姓名
实验课程:
实验项目: 数控加工中心编程与操作
实验日期: 年 月 日
预 习 简 要 |
|
实 验 目 的 |
|
实 验 设 备 |
|
实 验 内 容 |
|
零 件 图 |
|
数 控 加 工 程 序 |
|
实 验 步 骤 |
|
实 验 结 果 分 析 思 考 和 心 得 |
|
教师签名: |
实 验 三
学院实验报告
班级 学号 姓名
实验课程:
实验项目: 数控车床编程与操作实验
实验日期: 年 月 日
预 习 简 要 |
|
实 验 目 的 |
|
实 验 设 备 |
|
实 验 内 容 |
|
零 件 图 |
|
数 控 加 工 程 序 |
|
实 验 步 骤 |
|
实 验 结 果 分 析 思 考 和 心 得 |
|
教师签名: |
实 验 四
学院实验报告
班级 学号 姓名
实验课程:
实验项目: 数控电火花线切割机床编程与操作实验
实验日期: 年 月 日
预 习 简 要 |
|
实 验 目 的 |
|
实 验 设 备 |
|
实 验 内 容 |
|
零 件 图 |
|
数 控 加 工 程 序 |
|
实 验 步 骤 |
|
实 验 结 果 分 析 思 考 和 心 得 |
|
教师签名: |
实 验 五
学院实验报告
班级 学号 姓名
实验课程:
实验项目: 使用Mastercam软件构建二维图形并生成NC程序实验
实验日期: 年 月 日
预 习 简 要 |
|
实 验 目 的 |
|
实 验 设 备 |
|
实 验 内 容 |
|
零 件 图 |
|
数 控 加 工 程 序 |
|
实 验 步 骤 |
|
实 验 结 果 分 析 思 考 和 心 得 |
|
教师签名: |
实 验 六
学院实验报告
班级 学号 姓名
实验课程:
实验项目: 使用Mastercam软件构建三维曲面图形实验
实验日期: 年 月 日
预 习 简 要 |
|
实 验 目 的 |
|
实 验 设 备 |
|
实 验 内 容 |
|
零 件 图 |
|
实 验 步 骤 |
|
实 验 步 骤 |
|
实 验 结 果 分 析 思 考 和 心 得 |
|
教师签名: |
实 验 七
学院实验报告
班级 学号 姓名
实验课程:
实验项目: 使用Mastercam软件构建三维实体图形实验
实验日期: 年 月 日
预 习 简 要 |
|
实 验 目 的 |
|
实 验 设 备 |
|
实 验 内 容 |
|
零 件 图 |
|
实 验 步 骤 |
|
实 验 步 骤 |
|
实 验 结 果 分 析 思 考 和 心 得 |
|
教师签名: |
实 验 八
学院实验报告
班级 学号 姓名
实验课程:
实验项目: 三维曲面/实体零件NC程序生成生成实验
实验日期: 年 月 日
预 习 简 要 |
|
实 验 目 的 |
|
实 验 设 备 |
|
实 验 内 容 |
|
零 件 图 |
|
数 控 加 工 程 序 |
|
实 验 步 骤 |
|
实 验 结 果 分 析 思 考 和 心 得 |
|
教师签名: |
实 验 九
学院实验报告
班级 学号 姓名
实验课程:
实验项目: 三维曲面/实体零件数控在线加工实验
实验日期: 年 月 日
预 习 简 要 |
|
实 验 目 的 |
|
实 验 设 备 |
|
实 验 内 容 |
|
零 件 图 |
|
数 控 加 工 程 序 |
|
实 验 步 骤 |
|
实 验 结 果 分 析 思 考 和 心 得 |
|
教师签名: |