台 州 学 院
机 械 工 程 学 院
《互换性与技术测量》实验指导书
2014.8.3
目 录
实验一 尺寸测量
实验一(1)用立式光学计测量塞规
实验一(2)用内径百分表测量内径
实验二 形位误差及表面粗糙度的检测
实验二(1)用百分表测量零件径向圆跳动和径向全跳动
实验二(2)用比较法检测表面粗糙度
实验二(3)微机型万能工具显微镜测量圆度误差及同轴度误差
实验三 螺纹测量
实验一 尺寸测量
实验一(1) 用立式光学计测量塞规
一、实验目的
1. 了解立式光学计的测量原理。
2. 熟悉用立式光学计测量外径的方法。
3. 加深理解计量器具与测量方法的常用术语。
二、实验内容
1. 用立式光学计测量塞规。
2. 根据测量结果,按国家标准GB1957—81《光滑极限量规》查出被测塞规的尺寸公差和形状公差,作出适用性结论。
三、测量原理及计量器具说明
立式光学计是一种精度较高而结构简单的常用光学量仪。用量块作为长度基准,按比较测量法来测量各种工件的外尺寸。
图1为立时光学计的外形图。它由底座1、立柱5、支臂3、直角光管6和工作台11等几部分组成。光学计是利用光学杠杆放大原理进行测量的仪器,其光学系统如图2b所示。照明光线经反射镜1照射到刻度尺8上,再经直角棱镜2、物镜3,照射到反射镜4上。由于刻度尺8位于物镜3的焦平面上,故从刻度尺8上发出的光线经物镜3后成为一平行光束,若反射镜4与物镜3之间相互平行,则反射光线折回到
焦平面,刻度尺象7与刻度尺8对称。若被测尺寸变动
使测杆5推动反射镜4饶支点转动某一角度α(图2a),
则反射光线相对于入射光线偏转2α角度,从而使刻度
尺象7产生位移t(图2c),它代表被测尺寸的变动量。
物镜至刻度尺8间的距离为物镜焦距f,设b为测杆中
心至反射镜支点间的距离,s为测杆移动的距离,则仪
器的放大比K为:
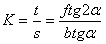
当
很小时,
,
,因此:
图 1
光学计的目镜放大倍数为12,
,
,故仪器的总放大倍数n为:

由此说明,当测杆移动0.001mm时,在目镜中可见到0.96mm的位移量。
四、测量步骤
1. 测头的选择:测头有球形、平面形和刀口形三种,根据被测零件表面的几何形状来选择,使测头与被测表面尽量满足点接触。所以,测量平面或圆柱面工件时,选用球形测头。测量球面工件时,选用平面形测头。测量小于10mm的圆柱面工件时,选用刀口形测头。
图 2
图 3
2. 按被测塞规的基本尺寸组合量块。
3. 调整仪器零位
(1)参看图1,选好量块组后,将下测量面置于工作台11的中央,并使测头10对准上测量面中央。
(2)粗调节:松开支臂紧固螺钉4,转动调节螺母2,使支臂3缓慢下降,直到测头与量块上测量面轻微接触,并能在视场中看到刻度尺象时,将螺钉4锁紧。
(3)细调节:松开紧固螺钉8,转动调节凸轮7,直至在目镜中观察到刻度尺象与μ指示线接近为止(图3a)。然后拧紧螺钉8。
(4)微调节:转动刻度尺寸微调螺钉6(图2b),使刻度尺的零线影象与μ指示线重合(图3b)。然后压下测头提升杠杆9数次,使零位稳定。
(5)将测头抬起,取下量块。
4. 测量塞规:按实验规定的部位(在三个横截面上两个相互垂直的径向位置上)进行测量,把测量结果填入实验报告。
5. 由塞规零件图(由学生自己设计、画出)的要求,判断塞规的合格性。
思 考 题
1. 用立式光学计测量塞规属于什么测量方法?绝对测量与相对测量个有何特点?
2. 什么是分度值、刻度间距?它们与放大比的关系如何?
3. 仪器工作台与测杆轴线不垂直,对测量结果有何影响?工作台与测杆轴线垂直度如何
调节?
4. 仪器的测量范围和刻度尺的示值范围有何不同?
实验一(2) 用内径百分表测量内径
一、实验目的
1. 熟悉测量内径常用的计量器具和方法。
2. 加深对内尺寸测量特点的了解。
二、实验内容
1. 用内径百分表测量连杆内径。
三、测量原理及计量器具说明
内径可用内径千分尺直接测量,但对深孔或公差等级较高的孔,则常用内径百分表或
卧式测长仪作比较测量。
1. 内径百分表
国产的内径百分表,常由活动测头工作行程不同的七种规格组成一套,用以测量10—450mm的内径,特别适用测量深孔,其典型结构如图1所示 。
内径百分表是用它的可换测头3(测量中固定不动)和活动测头2跟被测孔壁接触进行测量的。仪器盒内有几个长短不同的可换测头,使用时可按被测尺寸的大小来选择。测量时,活动测头2受到一定的压力,向内推动镶在等臂直角杠杆1上的钢球4,使杠杆1绕支轴6回转,并通过长接杆5推动百分表的测杆而进行读数。在活动测头的两侧,有对称的定位板8。装上测头2后,与定位板连成一个整体。定位板在弹簧9的作用下,对称地压在靠在被测孔壁上,以保证测头的轴线处于被测孔的直径截面内。
四、测量步骤
1. 用内径百分表测量内径
(1)按被测孔的基本尺寸组合量块。换上相应的可换测头并拧入仪器的相应螺孔内。
(2)将选用的量块组和专用侧块(图2中的1和2)一起放入量块夹内夹紧 (图2),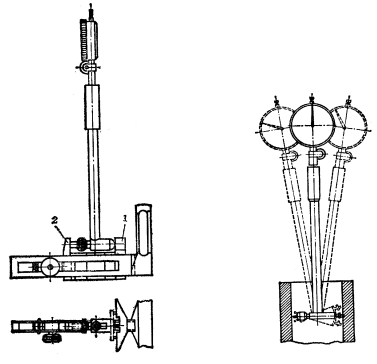
图2 图3
以便仪器对零位,在大批量生产中,也常按照与被测孔径基本尺寸相同的标准环的实际尺寸对准仪器的零位。
(3)将仪器对好零位
用手拿着隔热手柄(图1中的7),另一只手的食指和中指轻轻压按定位板,将活动测
头压靠在侧块上(或标准环内)使活动测头内缩,以保证放入可换测头时不与侧块(或标准环内壁)摩擦而避免磨损。然后,松开定位板和活动测头,使可换测头与侧块接触,就可在垂直和水平两个方向上摆动内径百分表找最小值。反复摆动几次,并相应地旋转表盘,使百分表的零刻度正好对准示值变化的最小值。零位对好后,用手指轻压定位板使活动测头内缩,当可换测头脱离接触时,缓缓地将内径百分表从侧块(或标准环)内取出。
(4)进行测量
将内径百分表插入被测孔中,沿被测孔的轴线方向测几个截面,每个截面要在相互垂直的两个部位上各测一次。测量时轻轻摆动内径百分表(图3),记下示值变化的最小值。根据测量结果和被测孔的公差要求,判断被测孔是否合格。
思 考 题
1. 用内径千分尺与内径百分表测量孔的直径时,各属何种测量方法?
实验二 形位误差及表面粗糙度的检测
实验二(1)用百分表测量零件径向圆跳动和径向全跳动
一、实验目的
1. 掌握用百分表测量径向圆跳动和径向全跳动。
2. 加深对圆跳动和全跳动定义的理解。
二、 实验内容
用百分表测量零件的径向圆跳动和径向全跳动。
三、 测量原理及计量器具说明
将百分表测头与零件被测部位接触,转动零件一圈,内径百分表指示表针所摆动的范围即为径向圆跳动误差。若零件转动的同时伴随着零件的轴向移动,则内径百分表指示表针所摆动的范围即为径向全跳动误差。
四、 实验步骤
1、径向圆跳动测量
1)将百分表固定在磁性表座上,使测头与零件被测圆柱面接触。零件缓慢转动一圈以上(一般转动2—3圈),记下表盘上指针的摆动的最大值和最小值,其指针摆动范围即为径向圆跳动误差值。
2)测头沿卡盘轴向移动3—5mm,继续上述步骤,测出另一表面的圆跳动误差值,并记录。
注意:百分表测头的位移方向应与被测表面测量点法向一致。
2、径向全跳动测量
1)将百分表固定在磁性表座上,使测头与零件被测圆柱面接触。零件缓慢转动一圈以上(一般转动2—3圈)并轴向移动,记下表盘上指针的摆动的最大值和最小值,其指针摆动范围即为径向全跳动误差值。
实验二(2)比较法检测表面粗糙度
一、 实验目的
加深对表面粗糙度的理解。
二、 实验内容
用粗糙度样块检测零件表面粗糙度。
三、 测量原理及计量器具说明
根据加工方法,通过目测或者借助放大镜将零件的加工表面与粗糙度表较样块表面进行比较,得出零件的表面粗糙度。
四、 实验步骤
1、将零件擦干净;
2、打开表面粗糙度比较样快;
3、在同一光照下,将零件表面与表面粗糙度样块目测(或在放大镜下)进行比较,记录下零件表面与粗糙度样板最接近的样板数据值(或记录下零件表面粗糙度值介于两块粗糙度样板之间的相应值)。
实验二(3)微机型万能工具显微镜测量圆度误差及同轴度误差
一、 实验目的
了解微机型万能工具显微镜测量形位误差方法。
二、 实验内容
使用微机型万能工具显微镜测量圆度和同轴度等误差。
三、 测量原理及计量器具说明
微机型万能工具显微镜以影象法和轴切法可按直角坐标和极坐标精确地测量零件的长度和角度,并可检定零件的形状。
1、测量范围及有关尺寸:
纵向行程:200mm
横向行程:100mm
圆台工作直径:213mm
平台工作尺寸:260×270mm
纵横向分度值:0.0002mm
2、工作原理
被测件置于照明光路中,由带有正象棱镜的主显微镜形成被测件的放大像,通过目镜中对准标记进行精密定位。而两次定位之间位移则由光栅装置精密测出,并将测量数据显示打印记录,或处理后再打印记录,从而完成非接触式的精密测量。
四、 实验步骤
1、 插上目镜
2、 装置照明设备
3、 测量形位误差
1)圆度测量
a)将薄圆柱形零件置放在工作台上,松开主显微镜架上的止动旋手,调整显微镜高低,使零件的影象位于视场中,调整物镜微调整环,使成象清晰。
b) 采集零件轮廓上的8个点(如图一所示),并根据所采集的8个点构造圆,然后点击“圆度”误差按钮,即可得到测量结果。处理结果在二维计算机辅助测试软件的“文字信息窗”内生成“圆度误差表”及圆度误差最大值。“图形信息窗”内生成圆度误差图形。
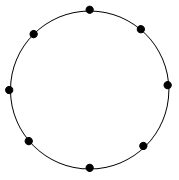
图 一
2)同轴度测量
a)将轴零件夹持于顶针架上,松开主显微镜架上的止动旋手,调整显微镜高低,使零件的影象位于视场中,调整物镜微调整环,使成象清晰。
b)点采集在两个相互垂直的轴截面上进行。先按图二(1)采集1-8点,然后将被测零件转动90°,按图二(2)采集9-16点。(其中1-4和9-11点为基准要素上的点;5-8和13-15点为被测要素上的点。)
c)数据采集完毕后点击“同轴度”形位误差按钮,再选择1-16点,即可得到“同轴度”测量结果。
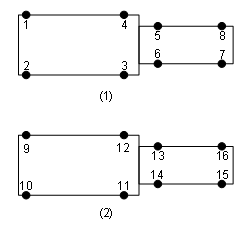
图 二
4、 记录实验数据。
5、 卸下工件,微机型万能工具显微镜断电,关闭计算机,汽油清洗工作台,盖上遮尘布。
实验三 螺纹测量
一、实验目的
熟悉测量外螺纹中径的原理和方法。
二、 实验内容
1. 用螺纹千分尺测量外螺纹中径。
2. 用三针法测量外螺纹中径。
三、测量原理及计量器具说明
1. 用螺纹千分尺测量外螺纹中径
图1为螺纹千分尺的外形图。它的构造与外径千分尺基本相同,只是在测量砧和测量头上装有特殊的测量头1和2,用它来直接测量外螺纹的中径。螺纹千分尺的分度值为0.01毫米。测量前,用尺寸样板3来调整零位。每对测量头只能测量一定螺距范围内的螺纹,使用时根据被测螺纹的螺距大小,按螺纹千分尺附表来选择,测量时由螺纹千分尺直接读出螺纹中径的实际尺寸。
图 1
2. 用三针测量外螺纹中径
图2为用三针测量外螺纹中径的原理图,这是一种间接测量螺纹中径的方法。测量时,将三根精度很高、直径相同的量针放在被测螺纹的牙凹中,用测量外尺寸的计量器具如千分尺、机械比较仪、光较仪、测长仪等测量出尺寸
。再根据被测螺纹的螺距
、牙形半角
和量针直径
,计算出螺纹中径
。由图2可知:

而
=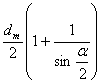

将
和
值代入上式,得:
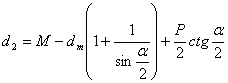
对于公制螺纹,
,则

图2 为了减少螺纹牙形半角偏差对测量结果的影响,应选择合适的量针直径,该量针与螺纹牙形的切点恰好位于螺纹中径处。此时所选择的量针直径
为最佳量针直径。由图3可知:

对于公制螺纹,
,则

在实际工作中,如果成套的三针中没有所需的最佳量针直径时,可选择与最佳量针直径相近的三针来测量。
量针的精度分成0级和1级两种:0级用于测量中径公差为4—8μm的螺纹塞规;1级用于测量中径公差大于8μm的螺纹塞规或螺纹工件。
测量M值所用的计量器具的种类很多,通常根据工件的精度要求来选择。本实验采用杠千分尺来测量(见图4)。杠杆千分尺的测量范围有0—25,25—50,50—75,75—100mm
图 3 图 4
四种,分度值为0.002mm。它有一个活动量砧1,其移动量由指示表7读出。测量前将尺体5装在尺座上,然后校对千分尺的零位,使刻度套筒管3、微分筒4和指示表7的示值都分别对准零位。测量时,当被测螺纹放入或退出两个量砧之间时,必须按下右侧的按钮8使量砧离开,以减少量砧的磨损。在指示表7上装有两个指标6,用来确定被测螺纹中径上、下偏差的位置,以提高测量效率。
四、测量步骤
1. 用螺纹千分尺测量外螺纹中径
(1) 根据被测螺纹的螺距,选取一对测量头。
(2) 擦净仪器和被测螺纹,校正螺纹千分尺零位。
(3) 将被测螺纹放入两测量头之间,找正中径部位。
(4) 分别在同一截面相互垂直的两个方向上测量螺纹中径。取它们的平均值作为螺纹的实际中径,然后判断被测螺纹中径的适用性。
2. 用三针测量外螺纹中径
(1) 根据被测螺纹的螺距,计算并选择最佳量针直径dm。
(2) 在尺座上安装好杠杆千分尺和三针。
(3) 擦净仪器和被测螺纹,校正仪器零位。
(4) 将三针放入螺纹牙凹中,旋转杠杆千分尺的微分筒4,使两端测量头1、2与三针接触,然后读出尺寸M的数值。
(5) 在同一截面相互垂直的两个方向上测出尺寸M,并按平均值用公式计算螺纹中径,然后判断螺纹中径的适用性。
思 考 题
1. 用三针测量螺纹中径时,有哪些测量误差?
2. 用三针测得的中径是否作用中径?
3. 用三针测量螺纹中径的方法属于哪一种测量方法?为什么要选用最佳量针直径?
执笔人:王金芳 审定人: